Inspired by a stunning homebuilt yacht, Ali Wood visits the Boat Building Academy to learn how any of us can become boatbuilders
How to become a boat builder in 40 weeks
Moored in Las Palmas, among dazzling white GRP yachts, Sweet Dreams is a boat I’ll never forget.
An elegant monohull crafted in wood from many different trees, the hull is western yellow cedar with Khaya mahogany veneer and the coachroof and cockpit varnished teak.
The interior is fitted out with Douglas fir, teak and oak. Every detail – from the rounded corners of the companionway hatch to the cream-painted tongue and groove panelling – has been planed, sanded and varnished to perfection.
The Bill Dixon one-design is a work of art, so it surprised me to learn that the owner, Roz Preston had built it by hand in Dorset, alongside late husband John. Was she a boatbuilder, I wondered?
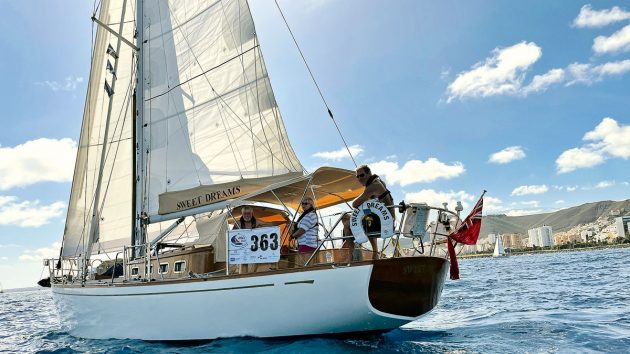
Homebuilt yacht Sweet Dreams sets out on the start of the ARC+ rally
No, she was a former special advisor to Tony Blair! Sweet Dreams was in fact a retirement project – which later crossed the Atlantic.
So how does one go from advising a prime minister to building a boat?
It all began, Roz told me, when she and John enrolled on a year-long course at the Boat Building Academy (BBA) in Lyme Regis.
This gave them all the skills they needed to get started on their seven-year labour of love.
Keen to find out more, I got in touch with the BBA, and was invited to join fellow students for a day of their five-day wooden boat restoration course.
The centre, nestled in Dorset’s idyllic Lyme Bay, runs a range of short courses from City & Guilds qualifications to traditional boatbuilding, GRP repairs and sailmaking.
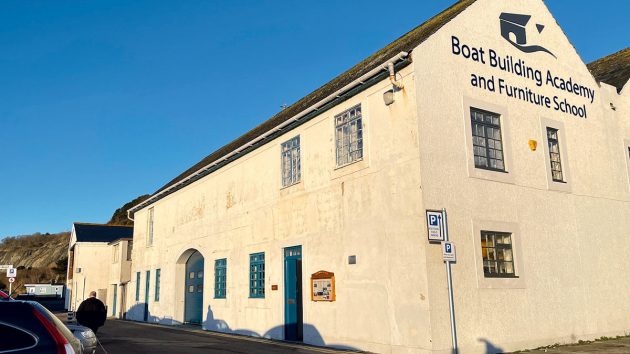
Lyme Regis Boat Building Academy
Longer courses include furniture making and the 40-week boatbuilding course.
A frost glistened on the beach and seagulls squabble as I pulled into the car park next to a decrepit clinker boat, which I later discovered belonged to student Ken Brand.
Students have the option to work on their own boats during the course, but sadly the bottom had fallen out of this one in transit, and it was deemed beyond economic repair.
“It would be possible if someone was willing to pay huge amounts of money,” said course tutor Matthew Law, “but there’s nothing there you’d want to keep. It would be a new build.”
Like many of the buildings in this picture-book Victorian resort, the two-storey Boat Building Academy has a fascinating history, having been built between the wars to house the RAF rescue motorboats, which TE Lawrence helped develop.

The boat restoration students learn how to make a scarf joint
The sound of machine-saws and hammers rang out across the car park, and as I entered the building, I was struck by the sweet smell of resin and sawdust.
Begoggled and wearing earmuffs, a student fed wood through a bandsaw, while others were planing, measuring and drilling.
On the floor were tins of epoxy and jigs supporting the wooden moulds of upturned hulls; on the walls were boat plans, whiteboards and clamps of every shape and size.
It looked fun, but my lesson this morning would start upstairs in the classroom.
Though I’d been warned to wear lots of layers, the sun poured into the room, illuminating the drill holes and scrapes on the desks that in any other learning establishment might have been considered graffiti.
The students
The students, both men and women, were of all ages, and from a range of backgrounds. Some were boat owners already.
Only one, Belinda, had actually worked in the trade as a finisher for Spirit Yachts.
All hoped to restore or buy a restoration boat in the near future and were keen to learn what to look for, and what to avoid – such as damaged caulking, splits, rot or poorly fastened plank ends.
Instructor Mike Broome, who it transpired had worked for Roz Preston, laying the teak decks of Sweet Dreams, was a former student himself who later moved to the area and set up his own boatbuilding business.
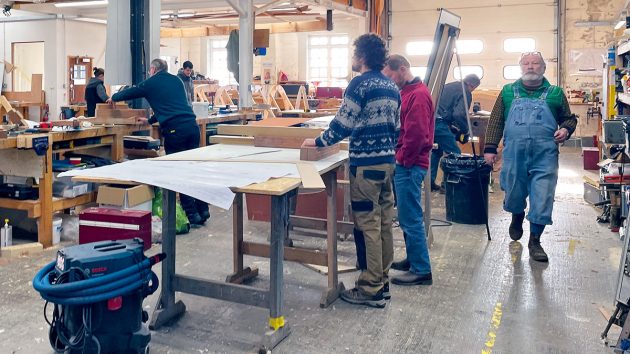
The students on the 40-week boatbuilding course
Mike gave me a folder of notes covering everything from hand tools to timber preparation, fastenings and sealant to planking, fitting out and finishing.
It seemed there was a lot to learn in just five days, but the emphasis of the course is on the practical element.
After two short classroom sessions, morning and afternoon, you move in to the workshop, and finish reading the notes in your own time.
There is limited accommodation at the academy, including the much revered Lookout room with sea views, though all the students were housed locally in B&Bs, with one even staying above the local pub.
Types of timber
“Wood is pure joy,” Roz had said to me when showing me around Sweet Dreams. “There’s immense satisfaction in turning a piece of raw timber into a door, for example, but it’s all curved, nothing is straightforward.”
This I learned in the first lesson with Mike, as he talked through the different types of indigenous timber suitable for boatbuilding.
The range is limited; you have chestnut, elm (when available), larch and Douglas fir.
However, larch and fir from the UK is often too fast grown to be suitable for planking stock. Ash, being perishable, is usually reserved for making smaller, more easily serviceable items.
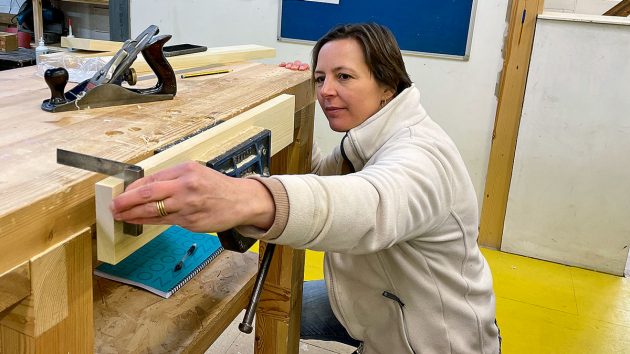
Belinda uses a set square to check the edge is straight
Spruce for spars tends to come from Sitka, Alaska, where the colder climate means growth is slower.
Even within species, the climate where the trees grow makes a difference. Slow growing larch from Siberia, for example, is stronger than its faster-growing European equivalent.
Commercially used hardwoods usually have a more complex cell structure and come from deciduous trees.
However, the prefix ‘hard’ is misleading. Balsa is a hardwood, but is extremely light and buoyant.
Softwoods, on the other hand, come from coniferous trees or trees with needle-leaves such as cedar and larch.
“What we’re looking for with timber is something that’s at least moderately durable,” explained Mike. “You have to think of all the labour, electricity and machinery involved in putting the boat together. You want to make sure that when it’s done it’s going to last as long as possible. That’s the best you can hope for.”
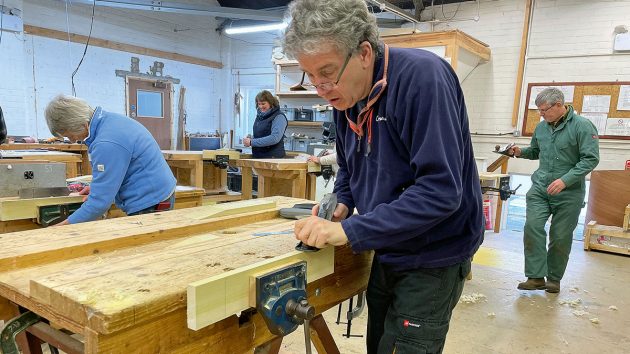
During the how to become a boat builder course, students learn about tools before progressing to woodworking
Of course, it would be impractical, time-consuming and expensive to make a boat only out of the most durable wood.
So while the hull might be made of something robust such as mahogany, sapele, teak, iroko or Douglas fir, you might use ash for belay pins, blocks and a tiller, which you can add a finish to, and keep an eye on, ready to replace when necessary.
Once felled, a tree is converted to timber baulks or planks, typically with a band or circular saw.
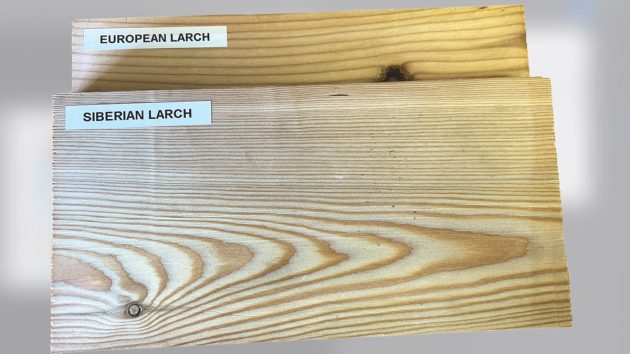
Larch from Siberia is stronger than European larch
However, it’s not just the type of timber that’s important for selecting wood, but the particular part of the tree, Mike explained.
“A tree is a conical structure that keeps adding bulk to itself as the year goes on. But there are bits of it that we really don’t want to use. When it starts out life as a sapling it’s trying to gain height and is full of nutrients. We don’t want to use the pith in the middle as it is prone to rot.”
Between the pith and the bark are three more layers, of which the heartwood, composed of dead cells, is the strongest and most usable part in boatbuilding.
So what does that mean for the boatbuilder?
Essentially different sawn pieces of timber have different properties and costs.
For example, a plain-sawn board, where the growth rings meet the face of the board at a tangent, is more susceptible to cupping during seasoning, whereas ‘quarter sawn’ timber, cut radially, is more expensive, but warps and shrinks less.
Sometimes the pith is left as a square piece or a ‘boxed heart’.
Seasoning
Once cut, the timber goes through a seasoning or drying process to reduce moisture. It shrinks – losing around 15-40% of its weight, until the moisture balance is equal to that in the atmosphere.
Air drying, where planks are stacked on battens, requires no technology but each inch of timber takes six to nine months (soft woods) and a year (hardwoods) to dry.
For boat interiors, a moisture content of 10-12% is needed, so kiln-drying, which is also much faster, is often used.
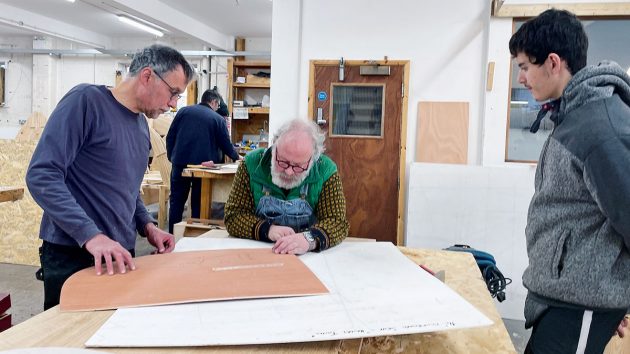
Examine the wood for defects before use
However, this makes the timber more prone to warping. Mike showed us several examples of warped wood – with defects including cupping, twisting and bowing.
Other faults to look out for in timber include shakes – a split or cleavage of the timber, knots (remnants of branches), which could come loose, and resin.
Also be wary of evidence of wood-boring beetles or wasps (ie holes).
To make life easier for the buyer, wood is graded to European Standards, and all of the above factors are taken into account.
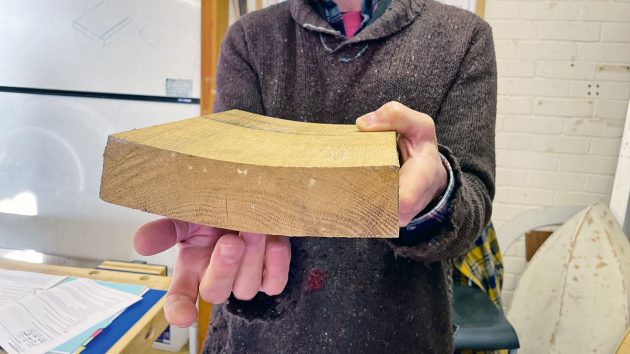
Wood can bow when heat treated
For best quality work you want ‘clear timber’ softwood or Grade 1 hardwood, but it’s still worth selecting your own timber and checking it over.
Interestingly, you can dry out wood too much.
Mike told us of an occasion when they ordered a batch of mahogany which had been set in a kiln. “When it arrived it was dried to death – about 6%! It was ridiculous. The first thing it did was change shape dramatically as it basically tried to suck all the moisture in West Dorset.”
Taking up water
I asked Mike whether it’s inevitable that a wooden boat will leak when first launched as it takes back moisture into the hull.
I recalled that PBO contributor Max LIberson had this issue, known as ‘taking up’, with his 1930s gaff rigger Wendy May.
Another contributor, Clive Robertson reported that his gaffer Andromeda “projected a 2in diameter column of water 20ft out her side“ when left on her trailer in a rising tide.
“How much the boat takes up water depends on the finish and how well it was built in the first place,” said Mike. “Softwood planking will take up faster, whereas hardwood planking will take longer due to the nature of the wood.”
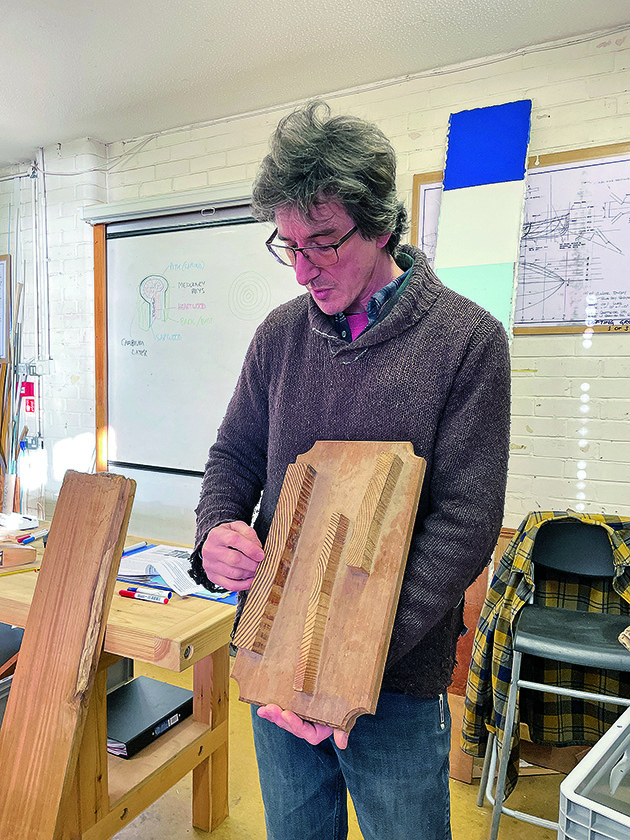
Mike shows how timber moves as it dries
He recalled a humorous incident with boatbuilder Gail McGarva, where they’d taken a Shetland double-ender to the Beale Park Show.
“We might get a bit wet,” she warned him, as they launched it on the slipway at the end of the lake.
“With a clinker boat it’s something of a self-fulfilling prophecy,” said Mike. “The boat had dried out completely, and had been oiled diligently, so there was no way the timber was going to take up moisture quickly.”
The water poured in, and of course the boat sunk lower in the water, and the effect was exponential.
These days, you can ‘cheat’ a bit with new builds, explained Mike.
If you’re going to dry sail them, first bruise a shallow groove and apply a thin bead of butyl rubber to make a gasket between the planks, before fastening, and that should keep the water out.
Plywood
Plywood is a popular choice for boatbuilders, being made from thin layers or ‘plies’ of wood veneer, which are glued together.
The adjacent layers have their wood grain rotated at 90° to one another.
Marine plywood can be any tropical hardwood, provided it’s at least moderately durable, but to carry the BS (British Standard) 1088 grade it has to use WBP (weather and boil-proof) glue.
Some come with a 15- or 25-year guarantee, which “sounds fabulous,” says Mike. “However, if you don’t seal the edges, moisture gets in, and if there’s frost, the ply will de-laminate.
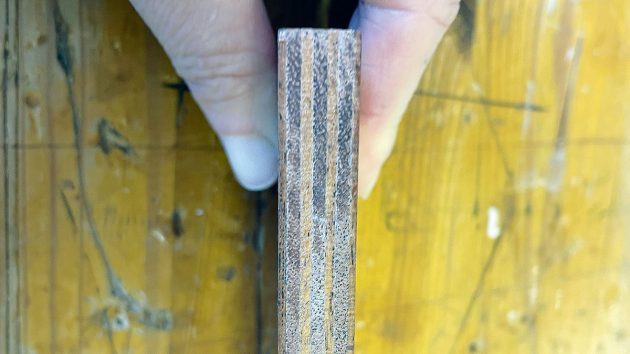
Don’t just buy on thickness. Ideally there should be at least five veneers. There are seven in this piece of khaya plywood
“Also, with economy plywoods, there can be voids, which can act like a pump, drawing moisture into the panel and allowing rot to start.”
Don’t just look at the thickness of the plywood, Mike warned; look for even thickness of the veneers. There should be at least five.
While you might see 6mm marine ply for sale, if 4mm of that is one single layer, and there are only three altogether, it’s not going to be very robust.
Marine borers
Once afloat, a wooden boat can still suffer damage from marine boring worms such as the teredo or ‘naval’ worm, a saltwater clam found increasingly in UK waters.
Mike recounted a story about an April fool advert that once ran in a wooden boat magazine.
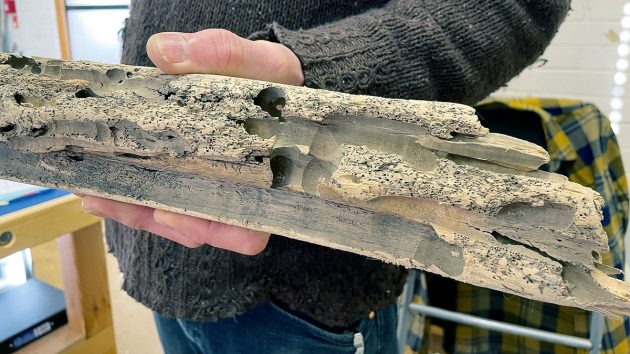
Look out for wood damaged by boring insects
The spoof purported there to be a marvellous wooden block which worked rather like a sacrificial anode, only instead of attracting stray currents away from the hull to prevent galvanic corrosion, it attracted marine borers.
The magazine was flooded with enquiries! Alas, no such thing exists.
Bending timber
Bending wood seems like one of life’s great mysteries. How does that timber that came from a solid, straight tree, become a beautiful curved piece of wood?
While small pieces can be cut to shape directly from a tree, most timber grown today produces long, straight boards. I learned there are several solutions.
For elm, ash and oak, steam-bending is excellent and requires a 45-60 minute period in the steam box per 25mm thickness.
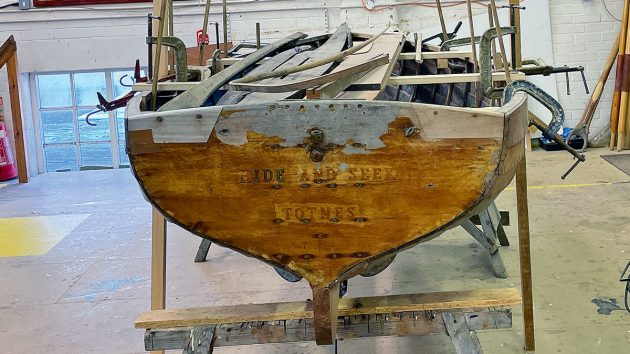
Students restore old boats – sometimes their own or ones belonging to other students and alumn
After the required time the steamed timber can be bent between blocks bolted to the ends of a metal strap, around a pre-made former or, in the case of a hull, can be bent directly into the boat in its final position.
Other options include laminating (glueing a number of veneers together), saw kerf cutting (making cuts and bending the wood towards them) and coopering, which begins as widening a joint but with bevels cut on the joining edges to form a curve or even a complete cylinder.
Continues below…
Boat wood: a complete guide for yacht owners
Boatbuilder and finisher Lyndon March explains which types of wood work best for different repairs and modifications on board
How to build a boat: Essential guide to building your first kit boat
You don’t have to be a boatbuilder to learn how to build a boat, argue Roger Nadin and Polly Robinson.…
Woodworking tools – a DIY boat owner’s guide to getting a professional finish
It’s not difficult to achieve a professional finish using woodworking machines and there are bargains to be had every day…
Best boat varnish: 7 top options for gleaming woodwork
Few things are as quintessential to the archetypal sailboat as gleaming, iridescent woodwork that is indicative of a recent coat…
Which glue?
Some adhesives are strong enough to bond wooden components on their own.
I was fascinated to learn about the more natural options including animal (made from hides, hoofs and bones of animals), fish (offal and skins) and casein (made from soured, skimmed milk curds), though these tend to be the preserve of the furniture makers.
Mike explained the difference between thermosetting – where heat changes a substance’s properties permanently, and thermoplastic, where it’s only temporary.
EVA Hot Melt is a useful thermoplastic. It can be used temporarily to bond plywood panels in place prior to filleting with thickened epoxy – and if you wish to remove the EVA, then you can apply a heat gun and scrape it off.
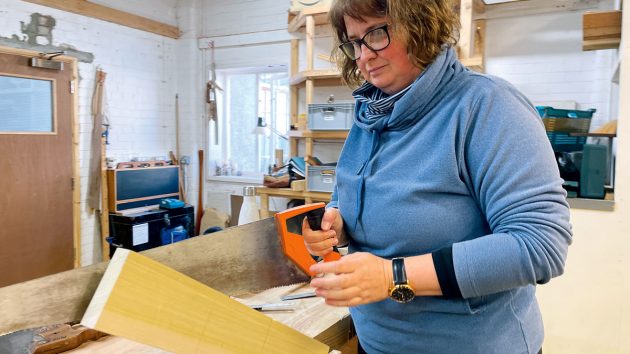
Student Kerstin uses a panel saw to cut the diagonal edge of her scarf joint
A whole range of thermosetting glues are used at the Boat Building Academy.
Throughout the course students become familiar with their properties – for example whether they cure through heat, moisture or mixing with a hardener – and which form (ie liquid, gel or paste) is best for which surface.
If you know your chemistry you can bond pretty much anything, Mike explained, citing his homemade archery bows as an example, which require maple wood to be bent and bonded onto carbon fibre.
Fillers too come in a variety of forms and are often used in wooden boat repairs.
“Sometimes chemicals are better than a wooden repair,” said Mike. “Glass cloth, resin and fillers are structurally fine, and are useful if you can’t get access to both sides of the hole when repairing modern wood constructed hulls.”
Another thing to be clear on is the difference between shelf-life (unopened) and pot life (opened), and mixing ratios.
I know from the PBO Project boat that getting this wrong – as I did with a primer coat – creates frustrating results.
“We use a lot of food words when teaching,” said Mike. “We’re looking for a ‘mayonnaise’ consistency or maybe ‘peanut butter’ – but smooth not crunchy! It might be too thin like ‘ketchup’ or if you use too much filler it ‘pulls like gingerbread’”.
Workshop
We next learned how to make a scarf joint, commonly used in boatbuilding to join two pieces of timber together when a longer piece isn’t available.
The students had learned how to sharpen and use hand-tools the previous day, and now they were putting it to practise.
I was thrilled to discover I’d also been allocated my own workbench and tool-kit.
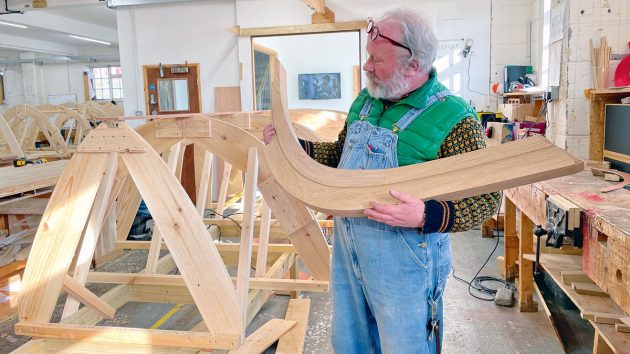
Matt holds an oak jointed stem which will form part of the 14ft glued clinker boat behind him
The tools for today were a tenon saw, panel saw, bench plane and chisel. Planes are generally available in metal or wood, with the latter being more expensive.
The best wooden planes have bases made from lignum vitae, a naturally oily wood which is self-lubricating Mike showed me how to adjust and use a bench plane, which I applied to each side of a strip of tulipwood until the shavings – or lack of them – indicated it was flat.
Although there are several types of planes for different tasks, one or two will cover most bases.
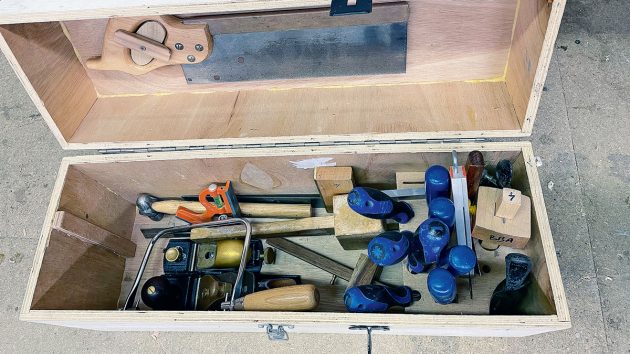
Every student gets a tool kit for the week
Using a rule and set square I checked the measurements, and then switched to a rip saw to rough-cut the diagonal edge.
It was relaxing and fun to be doing something with my hands.
As a child I used to like cutting wood in the garage with my junior hacksaw, and at secondary school I once decided to make a Victorian-style ‘planchette’ – a séance tool for writing messages from the dead. I’m glad to report it never worked!
It seemed there were even more choices of chisel than there are planes.
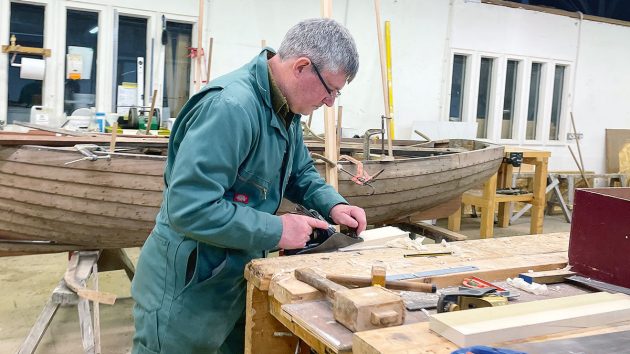
The course is hands-on, with the majority of time spent in the workshop
The firmer chisel is a general-purpose one, for example, whereas the bevel-edge is suited to lighter woodworking.
The paring chisel is used for slicing clean cuts, even in difficult grains. I should imagine after 40 weeks of boatbuilding the students will be well versed in all of these.
Less common shipwright tools include the draw knife, rove punch, caulking mallet, heavy maul and a slick.
Fastenings
In the afternoon session we learned about the broad range of fastenings available.
Mike explained that non-ferrous fastenings (copper and bronze) are best on a boat, even if they’re considerably more expensive.
Stainless steel, if not exposed to sufficient oxygen, can’t maintain its protective oxide layer and will corrode.
“You can imagine, if you’re going to bury stainless fastenings in wet timber – particularly oak, where you’ve got all that tannic acid reacting with the iron in the steel – it’s not a good idea,” he said.
There are many different types of wood screws, and we were given a table explaining the diameter, clearance hole and pilot hole for each gauge, which differed according to hardwood or softwood.
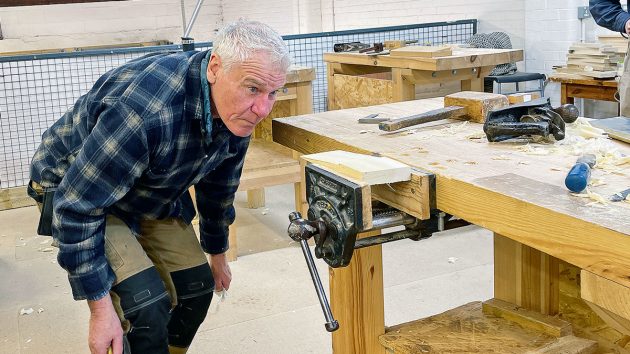
Ken inspects his work
Equally, there’s a vast range of nails, bolts, washers and nuts.
Not for the first time that day, I was awed by the minutiae of knowledge required to get to grips with boatbuilding.
Of course, with all the different fastenings on a wooden boat, you need to be aware of how metals react too.
Galvanic corrosion occurs when dissimilar metals come into contact while immersed in an electrolyte such as salt water.
Mike demonstrated how the current flows between them by pegging a strip of copper on one side of a saltwater jug and aluminium to the other.
His voltmeter read 395 millivolts.

Practising scarf joints
“I’m not introducing any current,” Mike emphasised, “This is just measuring what’s being produced.”
On a wooden boat, you might have a lead keel fastened with bronze keelbolts and bronze screws and copper nails holding together the planking, with heavier copper rivets securing the floors.
The trick, explained Mike, is to ensure your underwater metals are within 200 millivolts of each other, on the galvanic table.
This table determines the metal’s nobility in order of ‘most noble’ (cathodic) to ‘least noble’ (anodic).
Metals located further apart within the series are more susceptible to galvanic corrosion when combined.
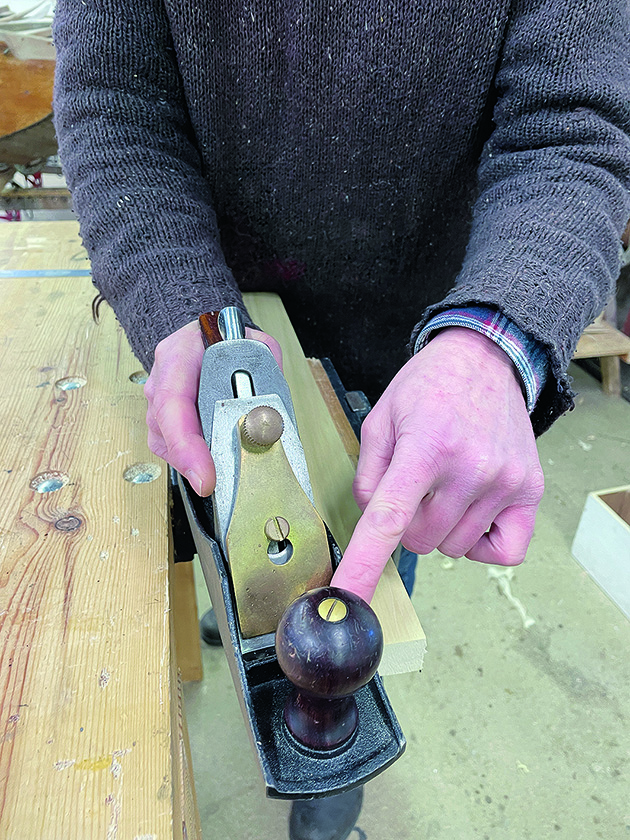
The bench plane is used to get a straight edge on the wood
Sacrificial anodes, made of aluminium, zinc or magnesium, are designed to corrode in order to protect other underwater metals.
Over-protection using too many zinc anodes can be detrimental on a wooden boat with metal fastenings.
The lignin in the timber around the fastenings is destroyed in a process known as alkaline degradation.
This is because the anode sets up a current and causes electrolysis, producing sodium hydroxide. This is commonly termed ‘nail sickness.’
Just the start of learning
The sessions had been a fascinating introduction to many elements of boatbuilding, and as one fellow student commented, the day had raised more questions than it answered (and it answered a LOT), such was the breadth of the subject.
It was thoroughly enjoyable and certainly made me want to go back and learn more.
Meet the students
Belinda Joslin
Belinda Joslin grew up in Ipswich sailing wooden boats that she built with her dad. After graduating in English and Sport at university, she moved into marketing.
However, after having three kids, she decided to change direction and became a finisher with Spirit Yachts.
One of the only women in the boatyard, she started the Instagram group Women in Boatbuilding, which is now a community interest company seeking to encourage gender diversity in the marine industry.
Ken Brand
Ken Brand is a retired firefighter and owns a 42ft Princess motorboat. He built his own house, converted two barns, and loves being hands-on.
He was inspired to do the course after inheriting an 80-year-old wooden clinker boat, which he brought to Lyme Regis for assessment.
Sadly it was deemed beyond repair, but Ken hopes to find another boat to restore.
During the week, Mike and Ken measured the old boat, and Mike created a lines plan and table of offsets for Ken, should he wish to recreate the vessel.
Kerstin Doefler
Kerstin Doefler is an international operations manager.
She spends every day at her laptop and decided she wanted to do something completely different.
One day she hopes to buy a boat to restore, so she chose to do the five-day course so she can get a better idea of what she’s looking for and understand the work required.
Pip Taylor
Pip Taylor is from Berkshire.
She’s building a 15ft rowing and sailing boat at home from a kit and decided the course would help her complete the project, particularly as the kit instructions were ‘absolutely appalling’.
She also has an old Mirror dinghy which needs some TLC.
She’s learned a lot of hand skills already on the course that she’s looking forward to applying when she gets back home.
Enjoyed reading How to become a boat builder in 40 weeks? 
A subscription to Practical Boat Owner magazine costs around 40% less than the cover price.
Print and digital editions are available through Magazines Direct – where you can also find the latest deals.
PBO is packed with information to help you get the most from boat ownership – whether sail or power.
-
-
-
- Take your DIY skills to the next level with trusted advice on boat maintenance and repairs
- Impartial in-depth gear reviews
- Practical cruising tips for making the most of your time afloat
-
-