The Secret 20 PBO project kit boat enters the final stages before the cosmetics are applied, as Jake Kavanagh reports
The Secret 20 is a beautifully-shaped wooden sailing yacht designed by Derek Ellard and available to the DIY enthusiast in a pre-cut kit. The brochure describes the boat as ‘the racing gaff cutter you’ve always wanted and in a size you can garage.’
Regular readers will know that the PBO editorial team began their own Secret 20 project from scratch back in 2016, using a kit delivered all the way from Australia where Derek and his team are based. When the relocation of PBO’s Poole office forced a reluctant clear out, the part-completed project was donated to the charity Oarsome Chance, which provides vocational education to school-excluded young people from across Hampshire.
Since its arrival at the Gosport workshop, the boat (named Harvey after a much-respected and greatly missed volunteer) has slowly taken shape under the expertise of boatbuilders Jon Carver and Jesse Doyle. Both these experienced instructors have tackled the more difficult jobs, whilst the Oarsome Chance students have helped with the basics.
Asking for advice
Last month the team had discovered a shortfall in the measurements between the foredeck and the cabin sides, but since then there have also been a few other minor problems, including the warping of the decorative veneer due to it drying out in the warm weather. Jon Carver dropped a line to designer Derek Ellard to ask for his guidance, something that is always quickly and readily given.
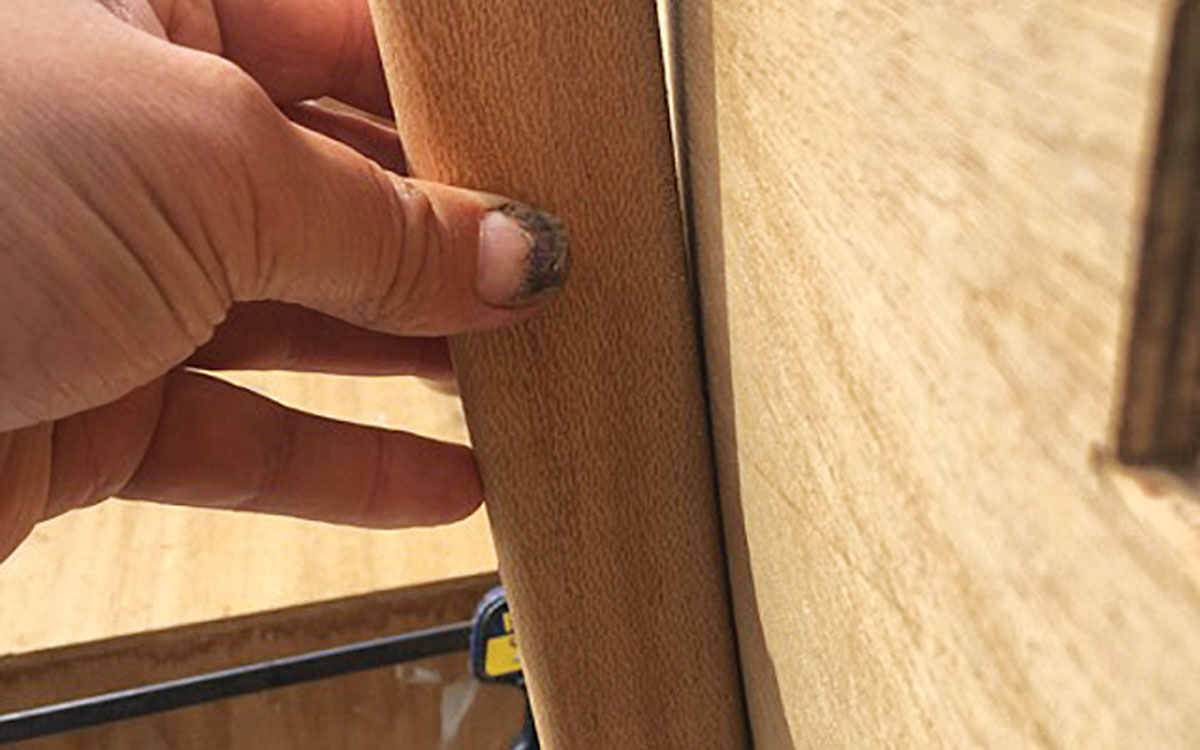
The oak veneer panelling cabin sides had warped from drying out: wetting and drying out again with convex battens clamped in place will straighten them up
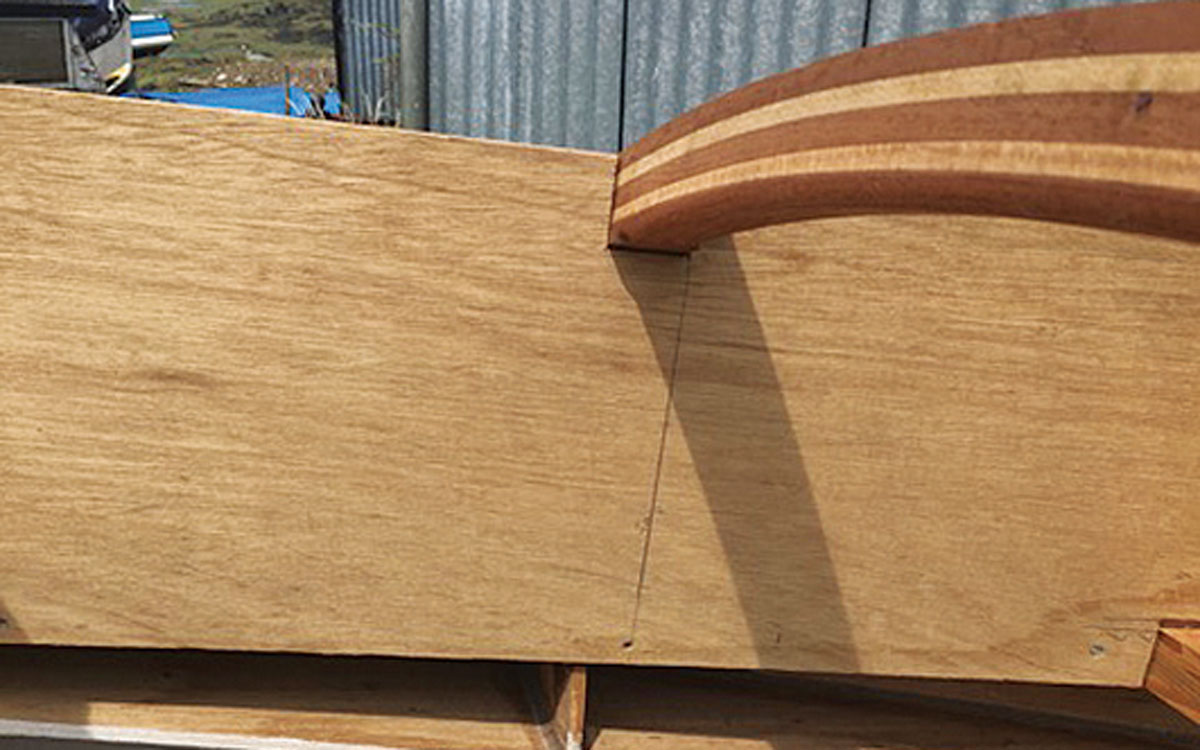
The structural alignment of the coachroof beams with the hull frames is essential for strength
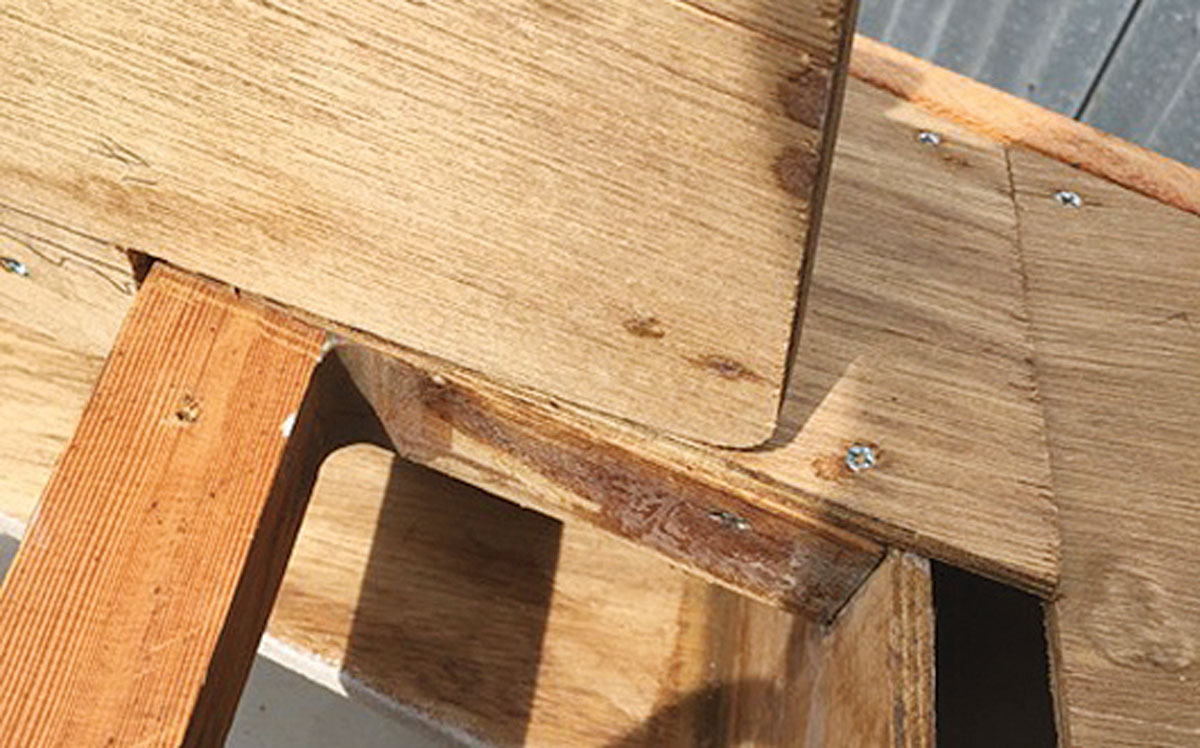
The OC team improvised a correction with the blessing of the kit designer Derek Ellard
“When we offered up the sides of the coachroof, the cutouts for the beams were not aligned with the hull frames,” Jon wrote. “So we increased the cutout at the forward end of the coach roof. There is now correlation between the beam and the frame. However, the foredeck, which has been dry fitted, doesn’t seem to extend far enough aft”
Derek’s reply was reassuringly straightforward. “The deck panels seem to be short – possibly our fault or the previous builders may have cut them back. Simply add another panel and glass tape the joint. There is no hard and fast rule as to how far the foredeck comes back.”
This is one of the joys of building in wood, especially when using a plywood and resin technique. Problems are usually very easy to fix, and modifications are also fairly simple, with a little planning, of course. Derek also suggested how the deck itself should be coated.
“At this stage it’s much easier to prime the deck with a two-pack high-build epoxy primer,” he wrote. “The first coat is thinned with an appropriate epoxy thinner and then abraded prior to fitting the cabin front and ‘dashboard’ trim. The first laminated beam can be set back a bit. Again, it’s not critical but the slots will put it in the right place. The position of the mast can also vary 20mm or 30mm and raked to fine tune the balance.”
Article continues below…
Project Boat update: Secret 20 completes deck fit-out stage
The Secret 20 is a beautifully designed classic sailing yacht that can be built from a kit, one of which…
PBO Project Boat Secret 20 update: Bulkheads and beams
Designed in Australia and built by enthusiasts all over the world, the Secret 20 packs grace and pace into her…
When it came to the warped silky oak veneer, which was pulling the plywood cabin sides out of shape, Derek had a simple solution: “First, thoroughly wet the side of the veneers with several coats of water. Then clamp vertical battens with a slight convex and gradually tighten them until the sides themselves are also slightly convex.
“You’ll need four or five per side. Allow to dry using a heat gun applied gently at regular intervals. Then, roll on thinned epoxy with accelerator (hardener). Lay this down wet-on-tacky for three coats. This should cure in 24 hours given reasonably warm and dry conditions but wait three days before removing the clamps. You can add a layer of fine [glassfibre] cloth over the veneer,” he said.
Derek also had some advice on achieving a good finish, especially when it comes to the oak joinery: “Remember to acetone-wipe all the joins between each section of silky oak, just as you would when preparing teak. This takes out the oils the wood has near the surface and makes coating much easier and longer-lived.”
Making the companionway entrance
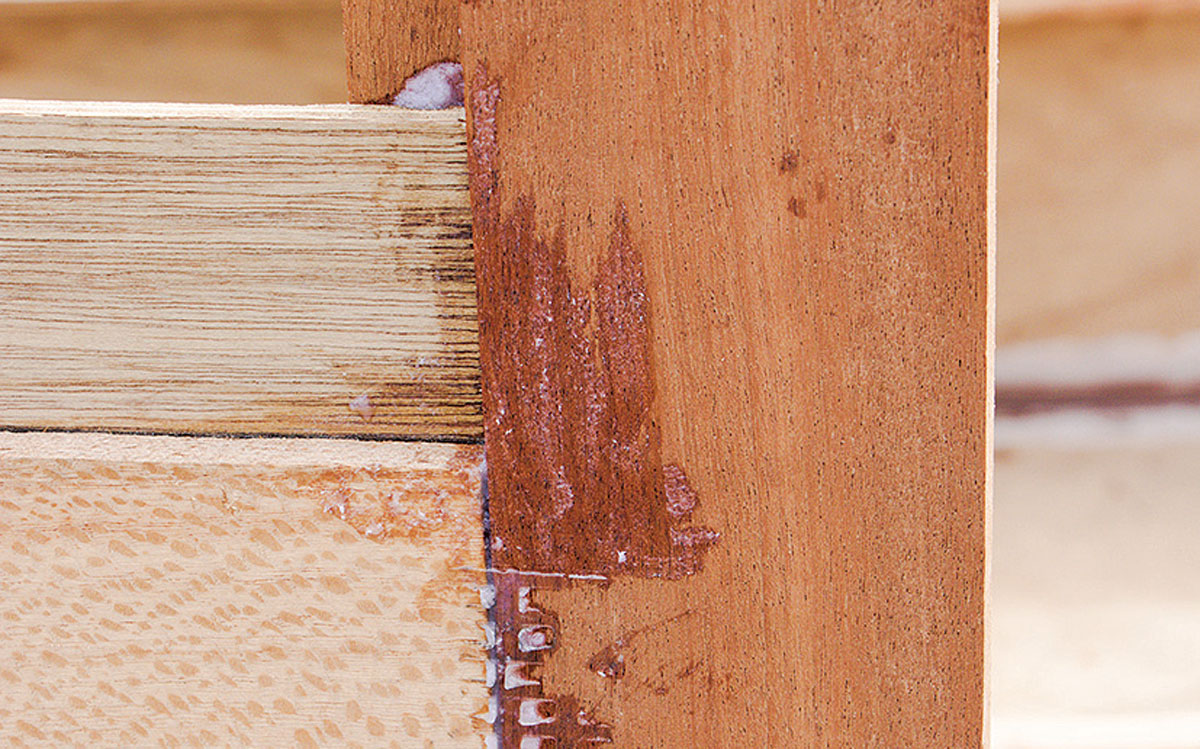
The corner support was created from two blocks of mahogany, cut to the thickness of the bulkhead. Photo: Jason Brodie-Brown
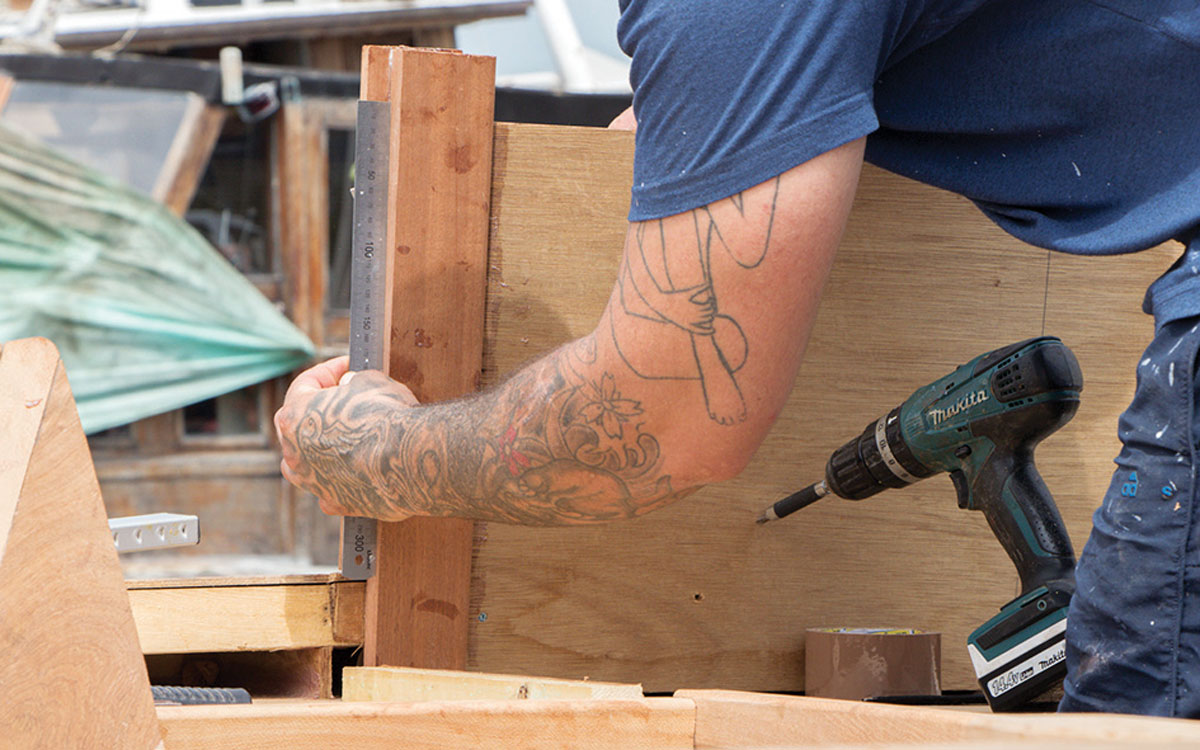
Jesse checks the measurements with a steel ruler, ideal as it gives a straight edge that resists being warped, unlike a flexible steel tape. Photo: Jason Brodie-Brown
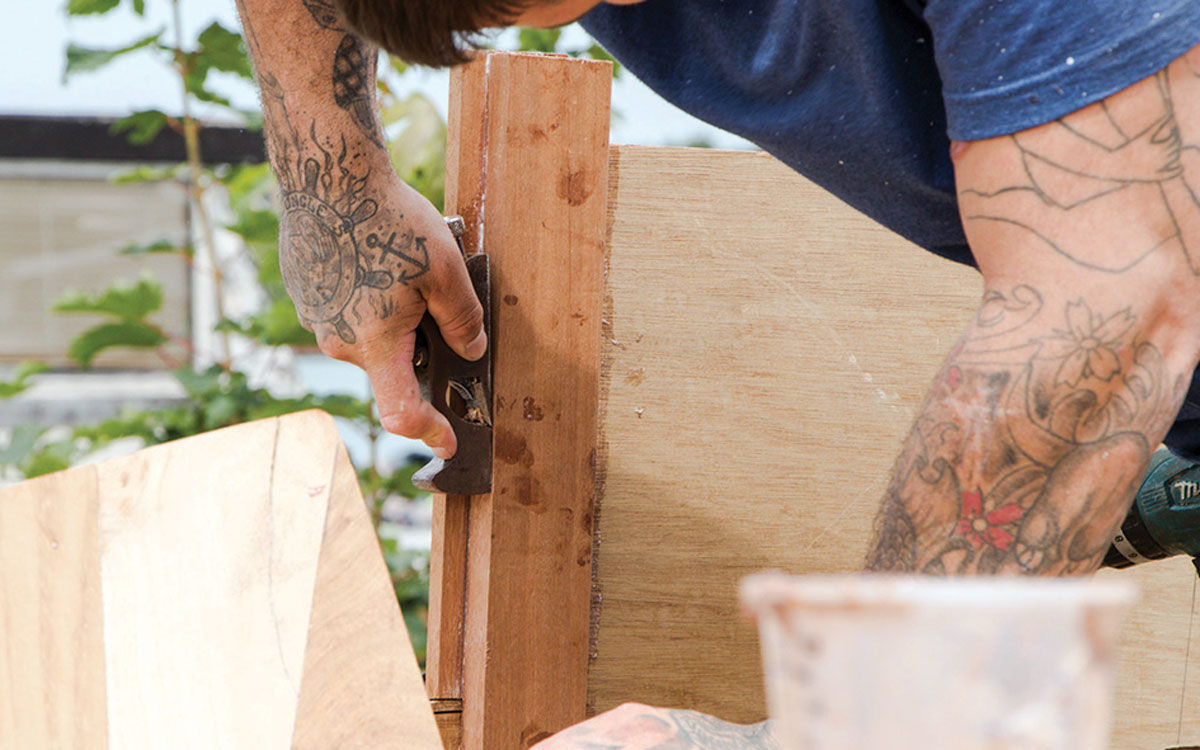
Any adjustments are made with a small hand plane or sharp chisel. With all tools, the sharper the blade the better the results. Photo: Jason Brodie-Brown
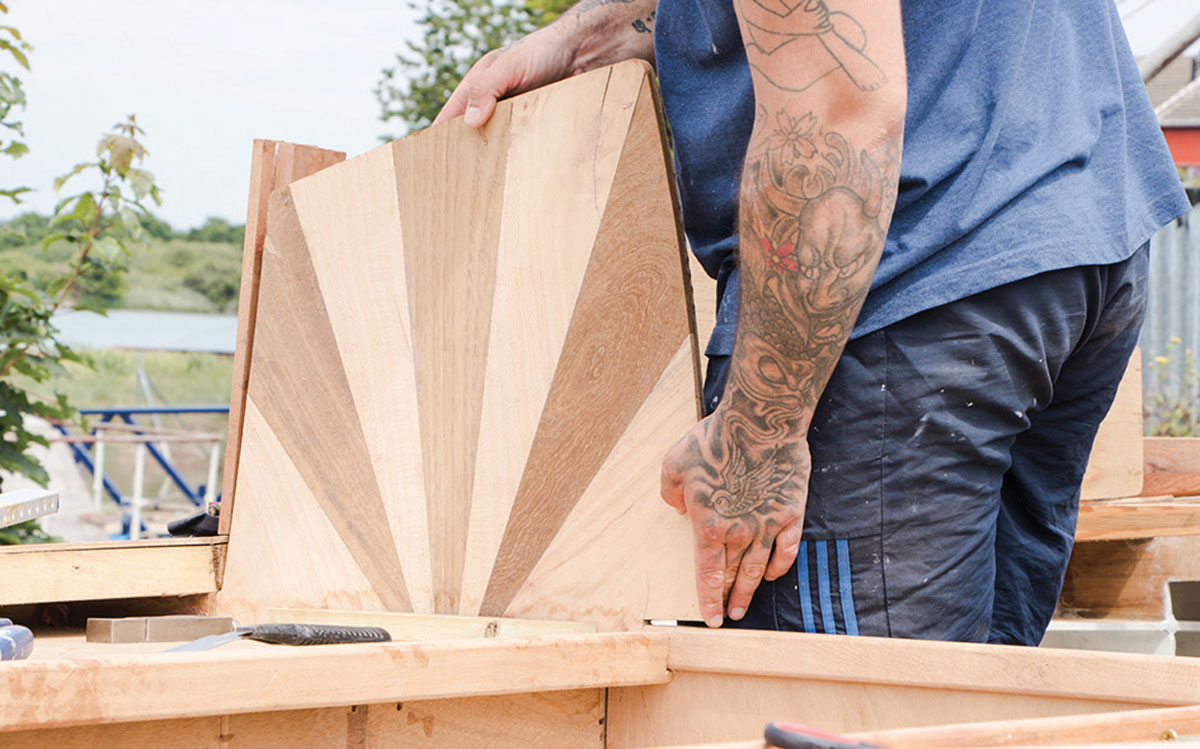
The bulkhead with its decorative veneer of coloured hardwood marquetry is offered up, and when a tight fit is achieved it is epoxied and clamped into place. Photo: Jason Brodie-Brown
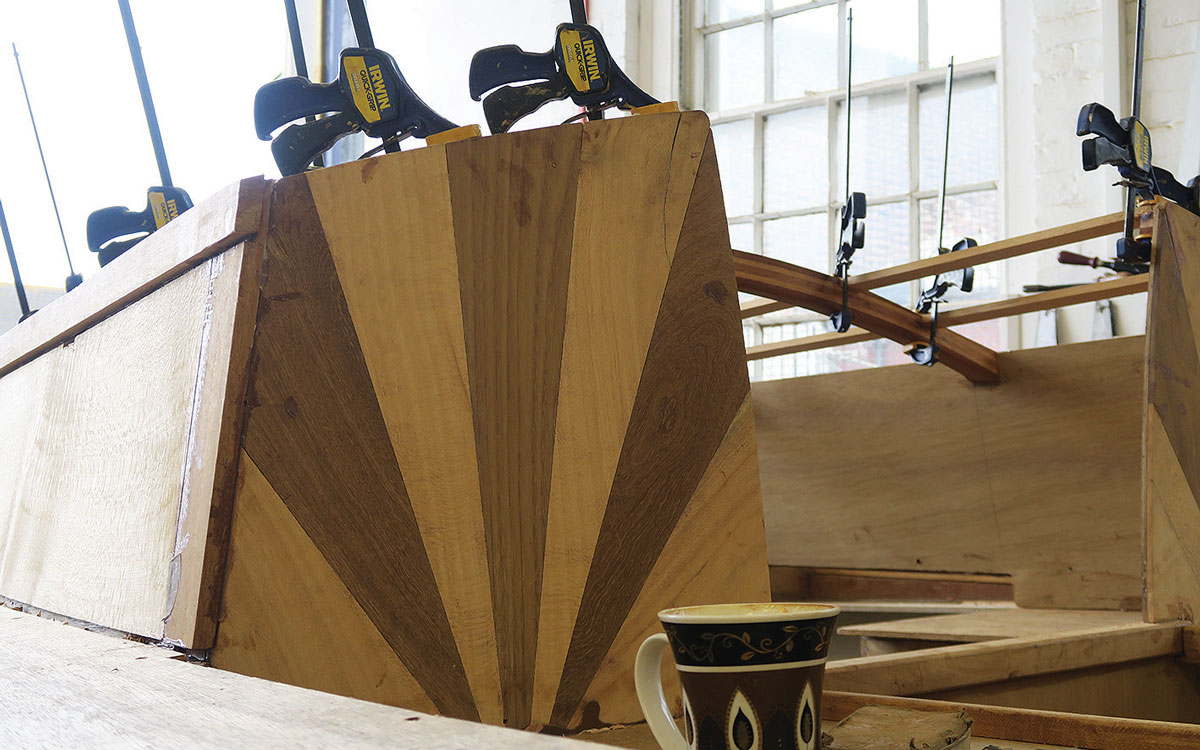
This bulkhead has a split, but it’ll be easily fixed with epoxy mixed with a little sawdust of the same wood. Photo: Jason Brodie-Brown
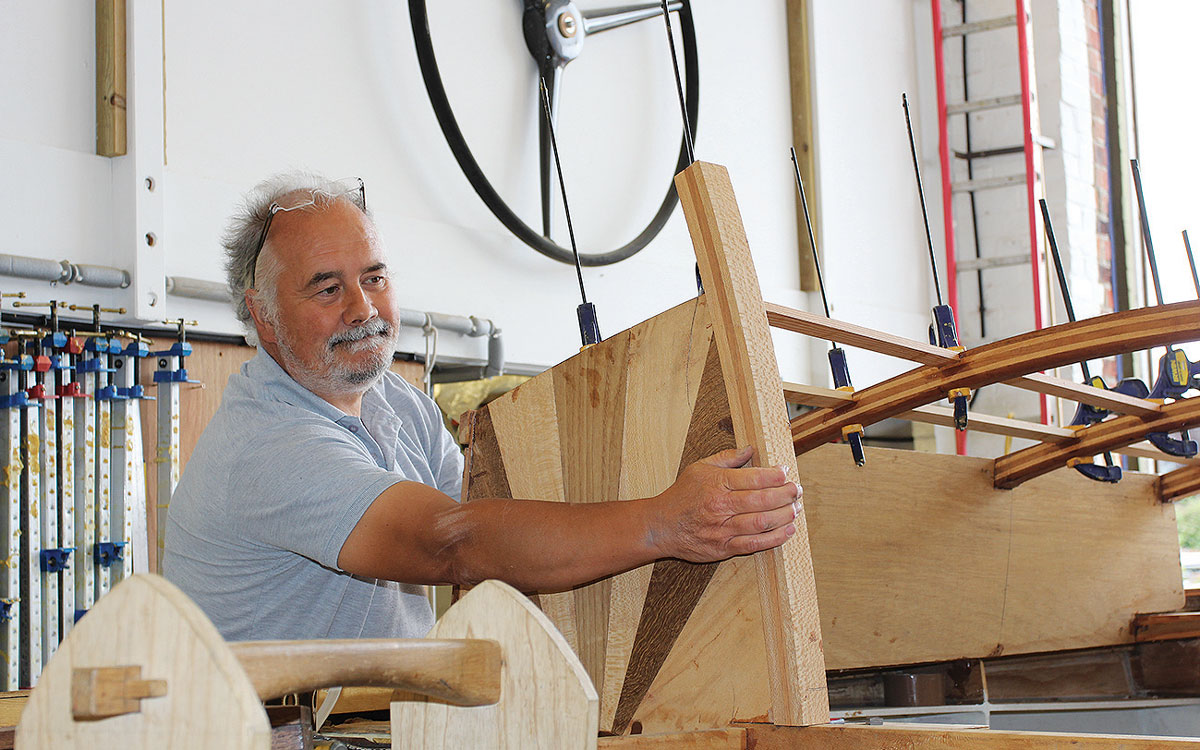
Jon Carver offers up the laminated and curved companionway trim, which will eventually take the hatch boards. Photo: Jason Brodie-Brown
Mast and sails
You always know when you’re getting near the end of a project when you start working on the rig. In the Secret 20’s case, this involves making four main spars – the mast, gaff and boom, plus the bowsprit.
All four octagonal-shaped lengths of Douglas Fir were supplied with the kit and simply need cutting to length, shaping and treating before being mounted and dressed with the necessary fittings.
Jon demonstrated the technique for turning a square section of timber into a perfectly circular profile. He used a spar gauge, which has two screws set into the middle at a ratio of 7:10:7. The screw tips just emerge through the bottom to allow them to put a shallow score mark in the surface of the spar.
The inside edges of the gauge are cut at an angle to sit astride the spar, and as the tool is run along each edge of the box section it leaves two scratch marks that will be used to guide a hand plane.
The tool will provide identically-spaced marks along each side of the spar so that, when planed, it will produce a perfect octagon. The octagon is then made into a hexadecagon by eye to produce equally placed 16ths, then 32 sides, and from here even a tapered mast can be shaped by rounded scrapers and/or sandpaper to be perfectly round.
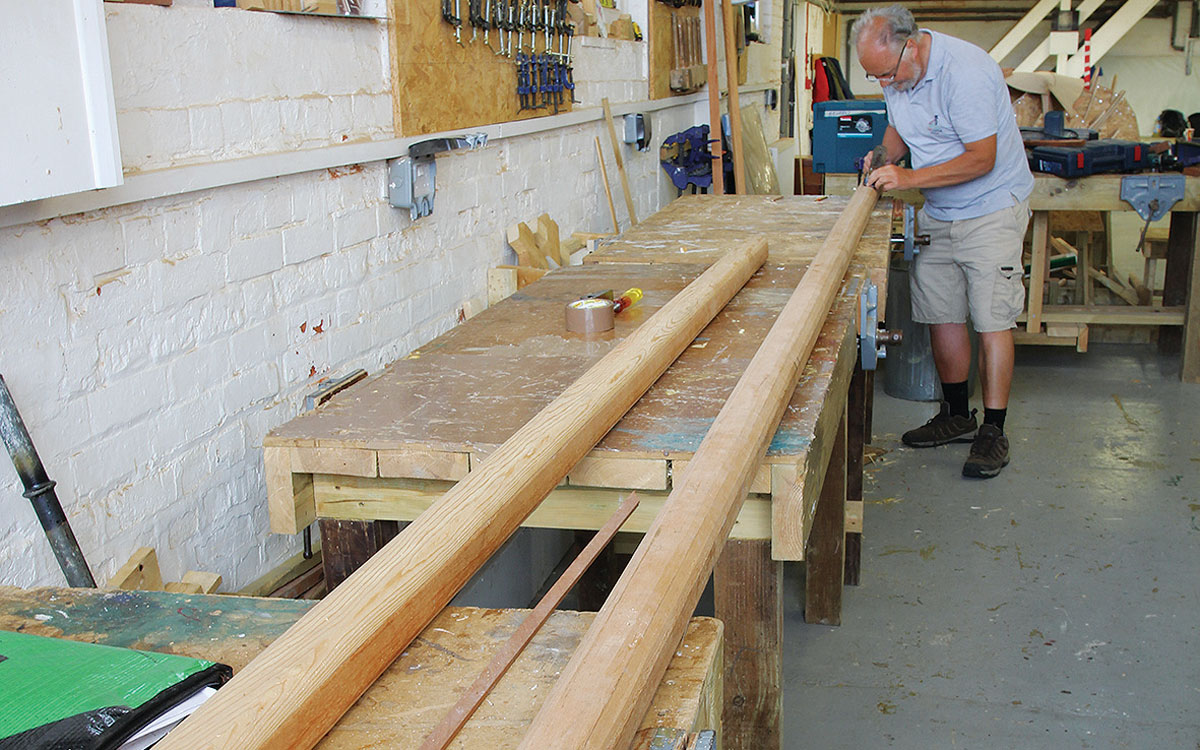
Long benches are ideal for working on spars, of which there are four for the Secret 20: mast, gaff, boom and bowsprit – all fashioned from Douglas fir
The boom is hollow with solid ends but is comparatively heavy. It is not designed to be fully rounded. The Secret 20 doesn’t have a vang (kicking strap) so the weight of the boom helps sail shape in light airs. “Once we have made the spars, we probably won’t epoxy them,” Jon said.
“Some people do, but if the epoxy coating is broken, it has the habit of trapping water underneath and can promote rot. We prefer to simply use a UV stable, single-pack varnish. This coating is flexible and easy to sand back and replace if damage occurs.”
The sail plan features a gaff cutter design, with the removable bowsprit emphasising Harvey’s classic yacht inspiration. (There is an added advantage in that marina fees can be reduced as the bowsprit adds a good 2m to the length overall!). There is also the option to fly a large gennaker in light airs.
The sail cloth is being supplied by Contender sails, with the option of either a traditional tan, or an old school cream. The sails are being made by a volunteer who has worked with the charity on various canvas projects and is looking forward to the challenge. More on that next month.
Installing the cabin front
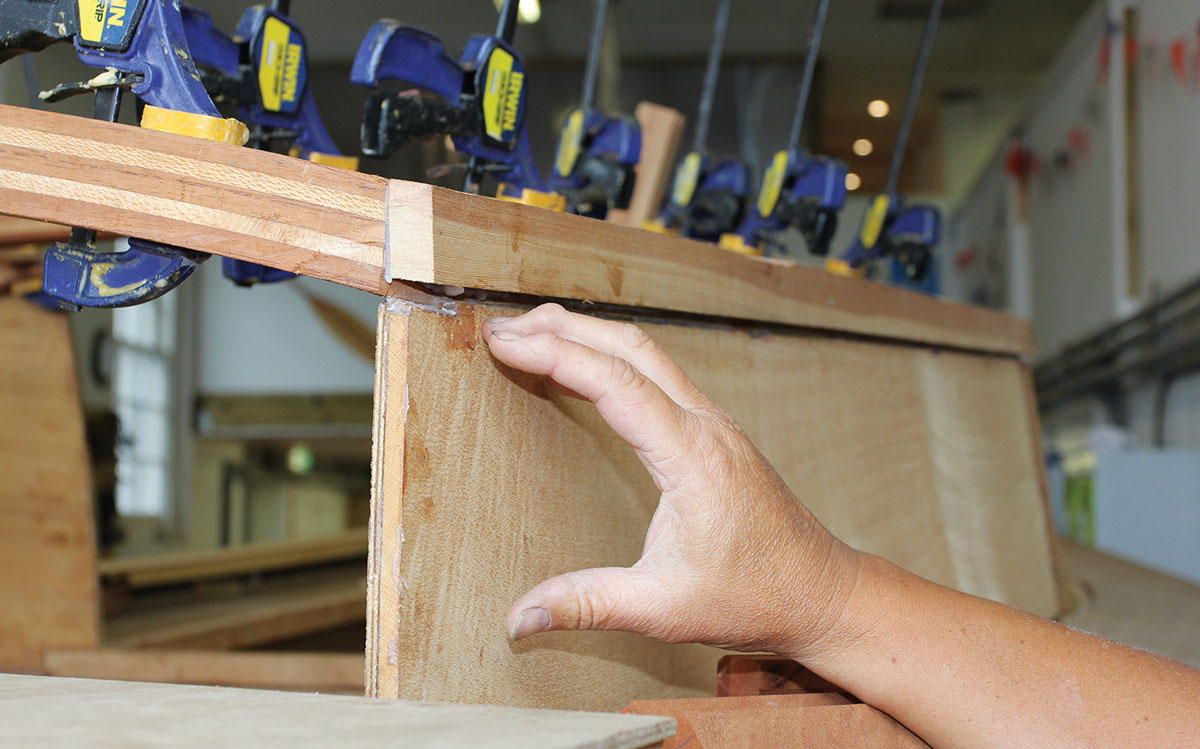
The cabin is made from 6mm ply overlaid with a thick (8mm) veneer of Australian Silky Oak, a recurring theme in this build
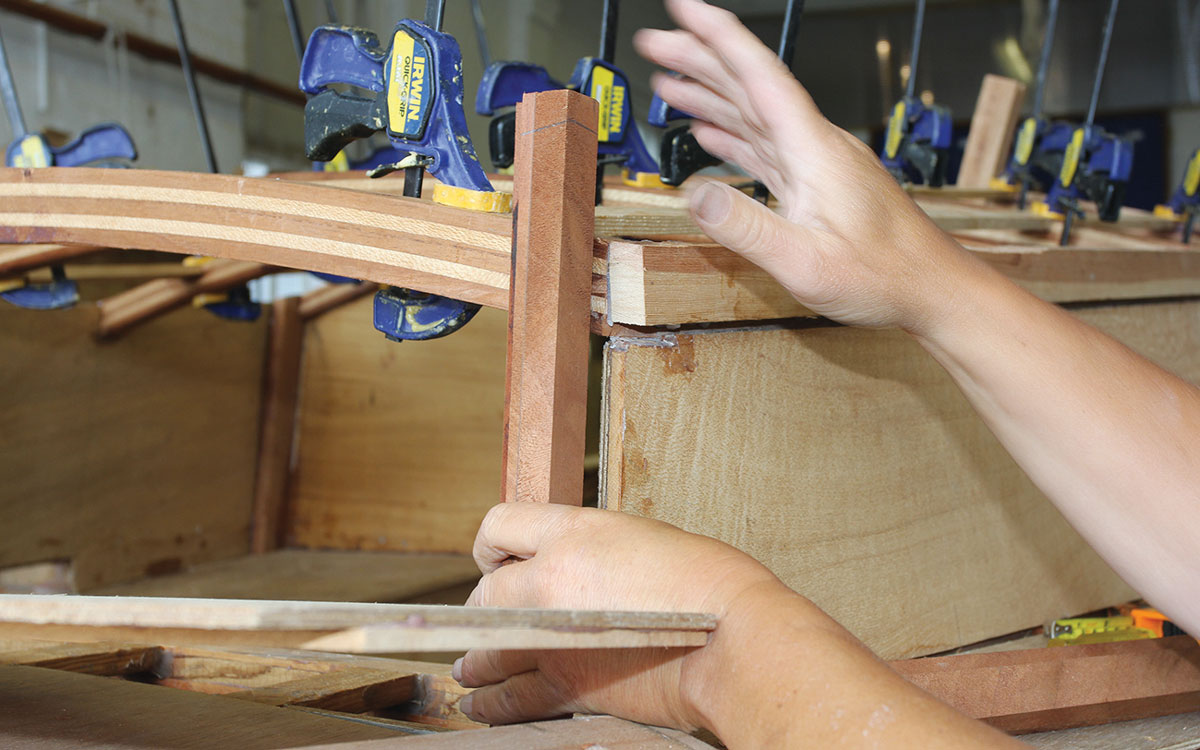
Similar to the rear cabin bulkhead, the forward end starts with a corner post made from two blocks of hardwood glued together with thickened epoxy
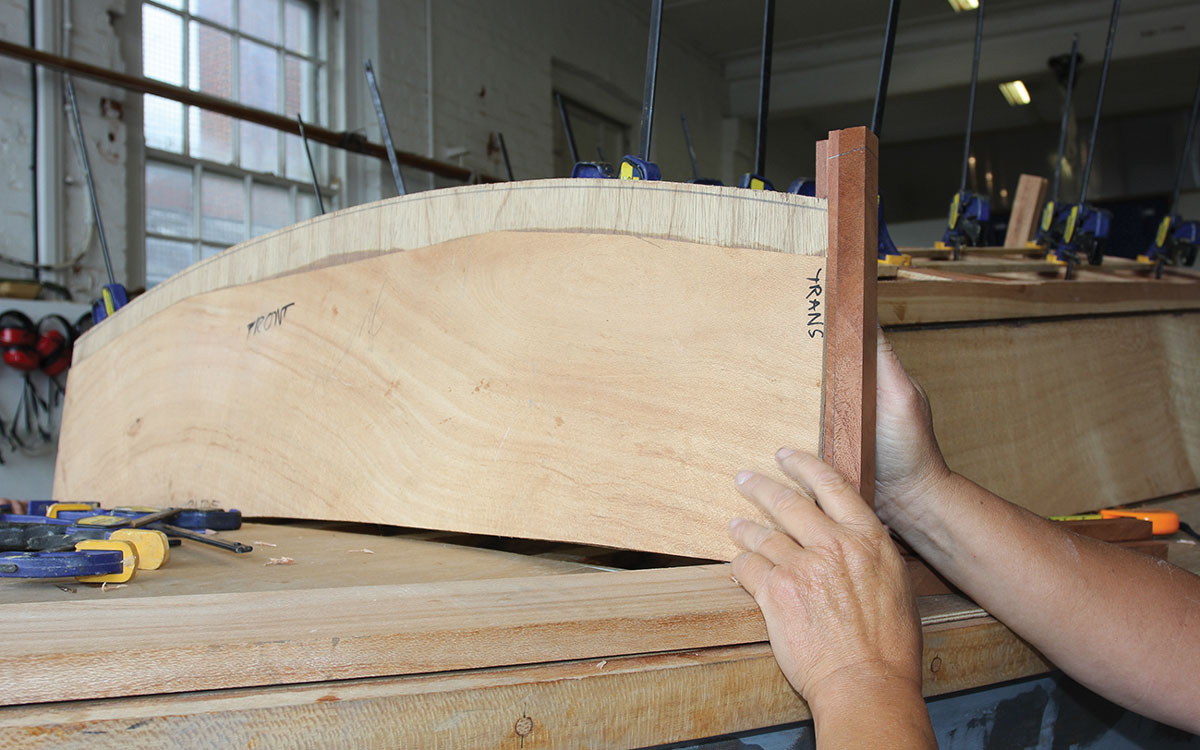
The cabin front is then manoeuvred into place and trimmed to fit. Note the curve top and bottom, which will be filleted into place
Power to the people: Torqeedo and Lifos
The Secret 20 features an easily driven hull, one of the reasons it sails so well, so doesn’t require a large engine. Instead, mechanical power has been kindly donated by the German electric outboard manufacturer Torqeedo.
The engine is being provided is the latest Travel 1103 C model. Described as providing the equivalent of a 3hp petrol engine, the new Travel 1103 C is a direct-drive electric outboard with its own integrated 915Wh lithium battery.
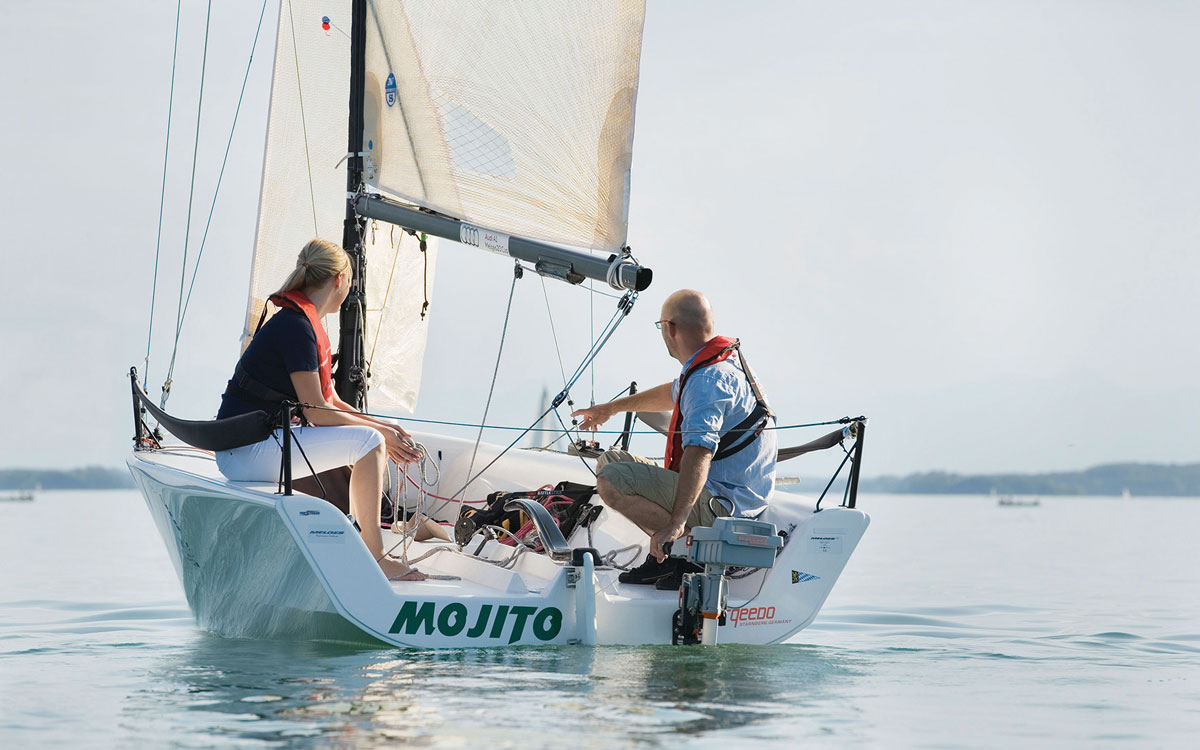
Torqeedo Travel 1103 C features a direct drive motor and is claimed to be equivalent to a 3hp petrol engine
Engineers have been at work to make an already quiet engine even quieter, with the motor now spinning at just 33dB without the electronic whine for which it had previously been known.
“The new motor now features direct drive technology that makes it really quiet,” said Torqeedo’s Oliver Glueck. “We have also increased the motor power by 10%, and two types of propeller are available, one intended as a ‘weed cutter’ for inland waterways.”
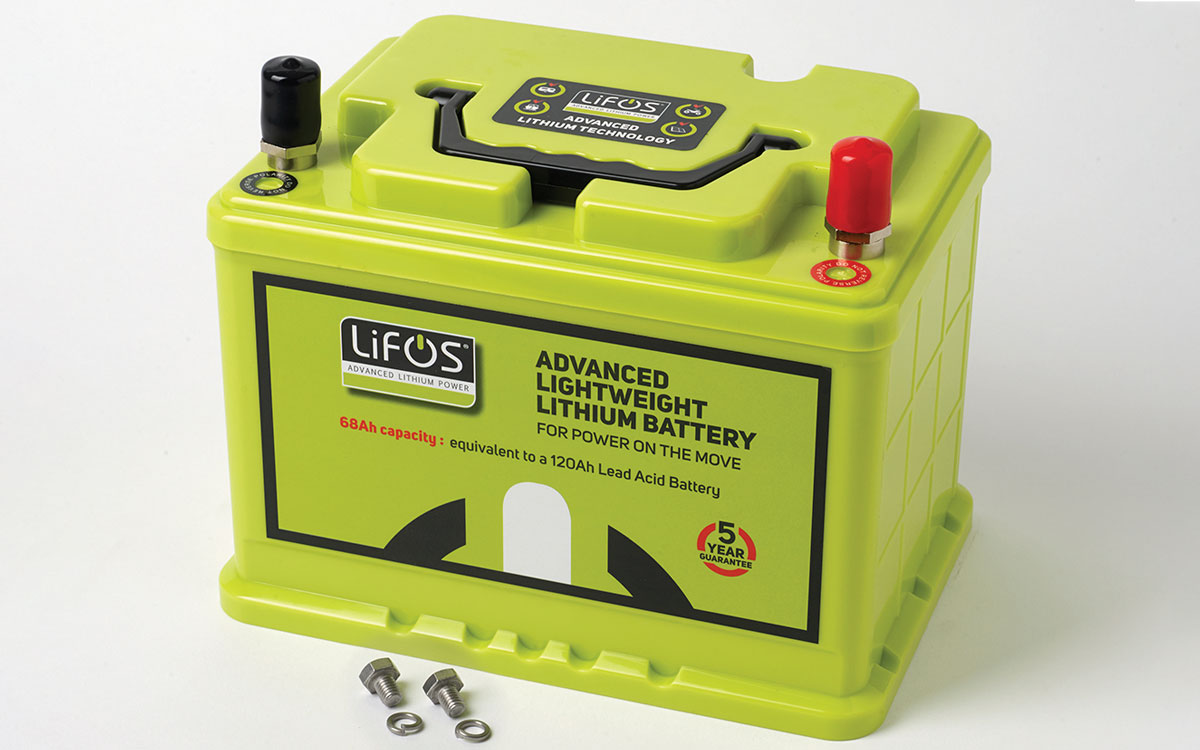
The donated Lifos lithium-ion phosphate battery has the same power equivalent as a 120Ah lead-acid
The electrical theme continues with another welcome donation, this time from Solar Technology International, suppliers of the new Lifos battery.
The battery destined for Harvey is rated at 68Ah, but because lithium-ion phosphate can be deep cycled to 90% drain, it is equivalent to the power available in a 120Ah lead acid battery. It weighs just 7.8kg, which is around 77% less than a traditional leisure battery and can be used in any orientation without special ventilation.
Circling the square
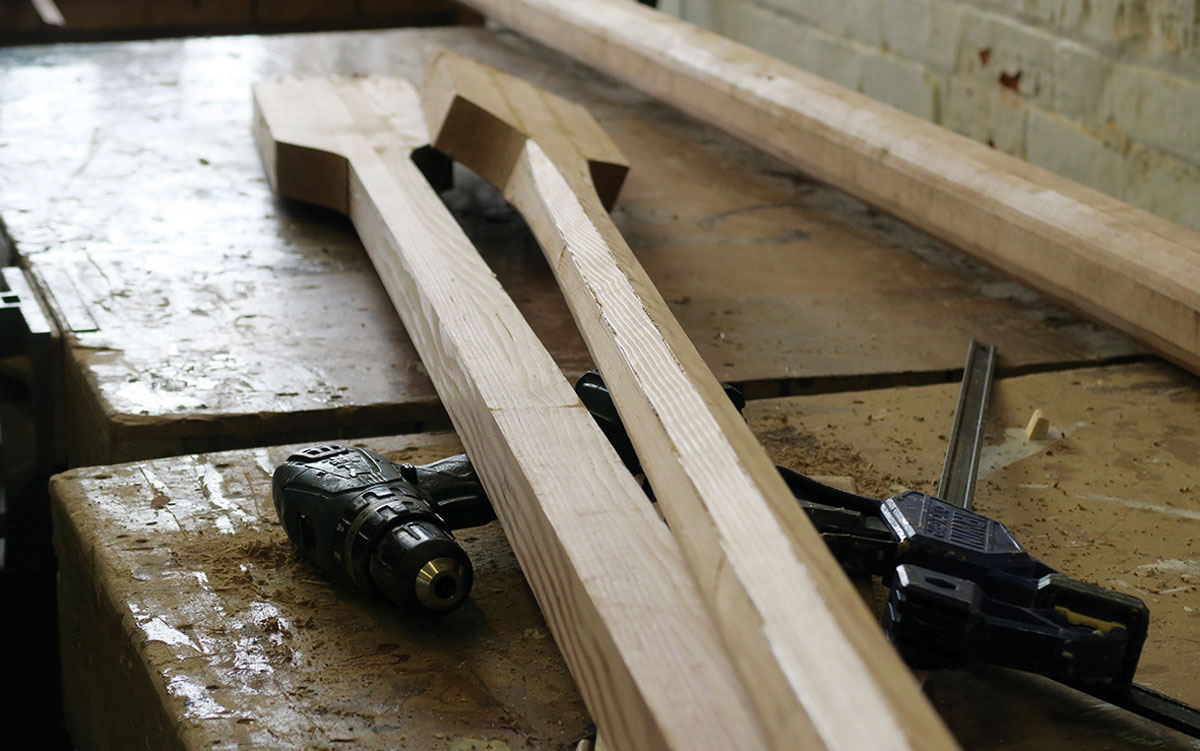
Masts, spars and paddles start off as squares, before being shaped to an octagon, and from there, if necessary, to a perfect circle
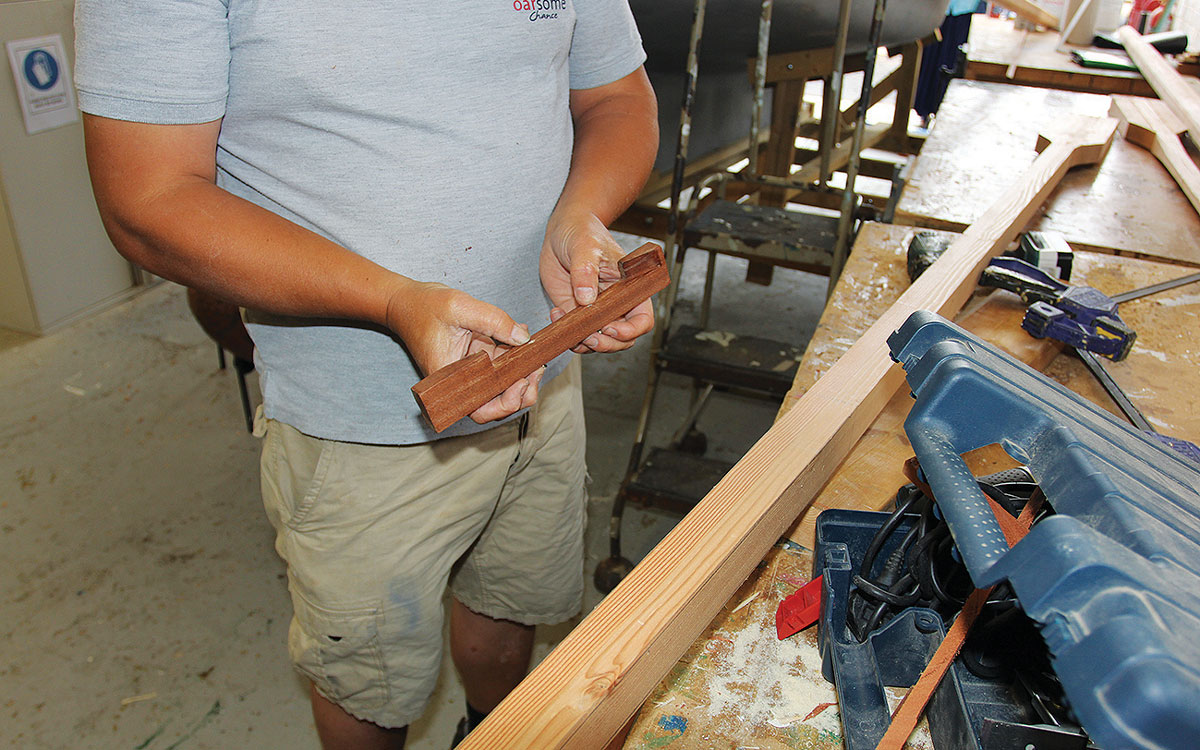
This spar gauge is the secret weapon. Note the two screws set into the timber and how their tips just protrude clear at the bottom
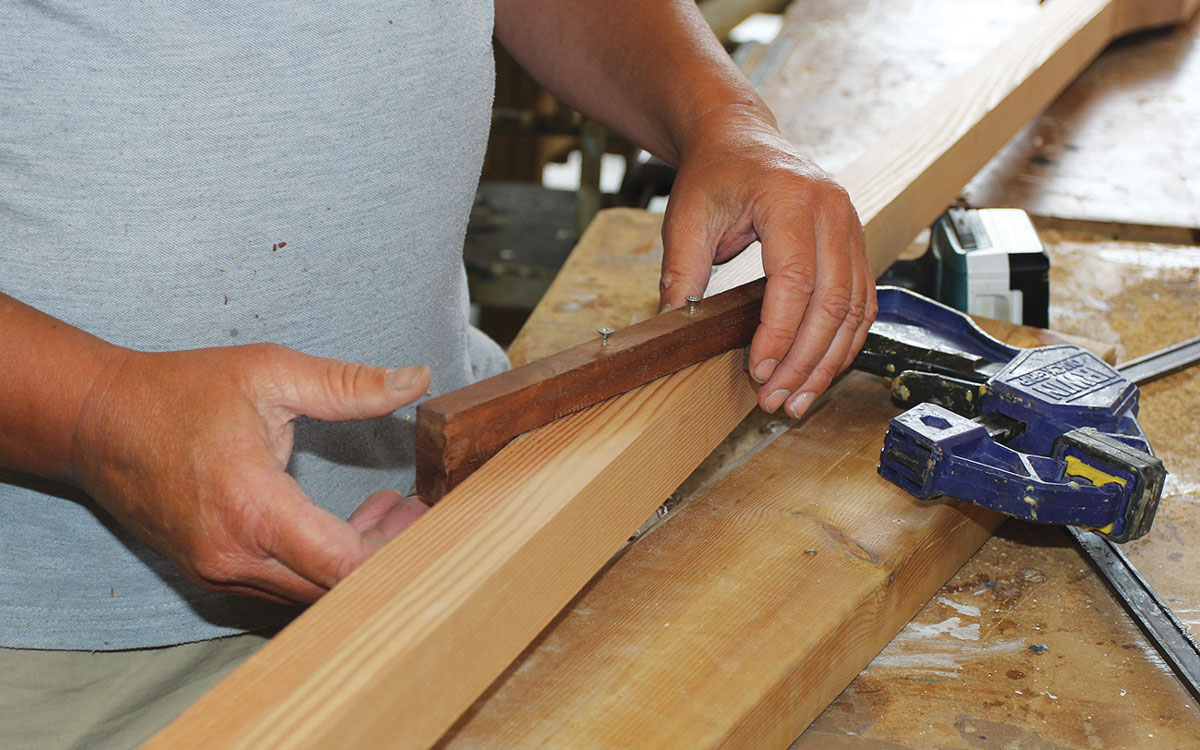
The gauge is laid onto the square box section and run along the full length of all the sides. The ratio stays consistent even if the spar tapers
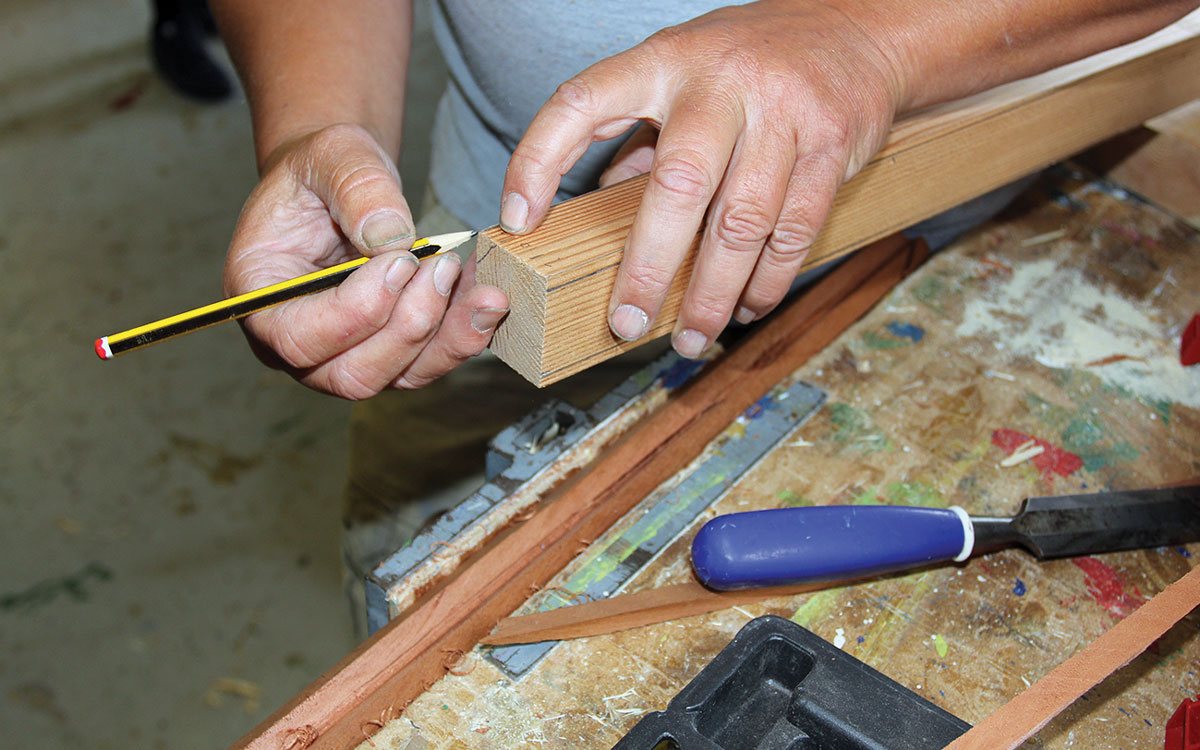
The score marks can be highlighted by running a sharp pencil along them. This spar will soon become a perfect octagon
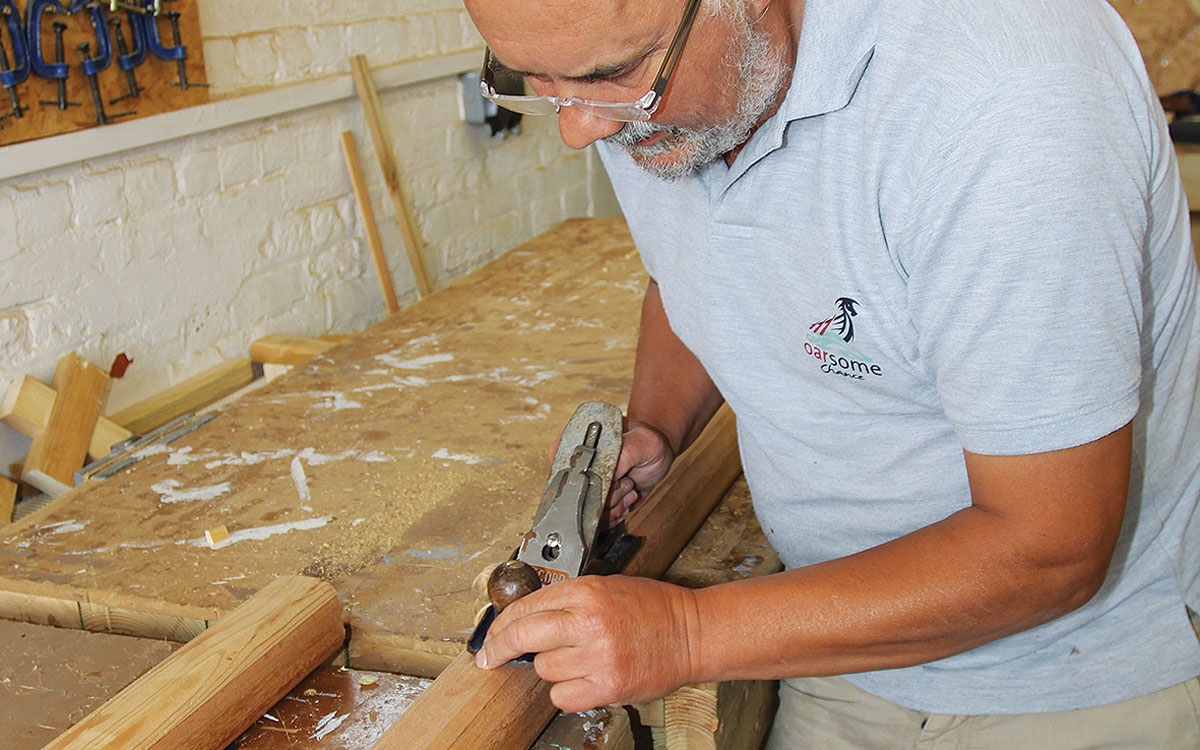
Jon now carefully runs his hand plane along the marks to remove the excess wood only to the lines, and no further. It is careful work but gives great results
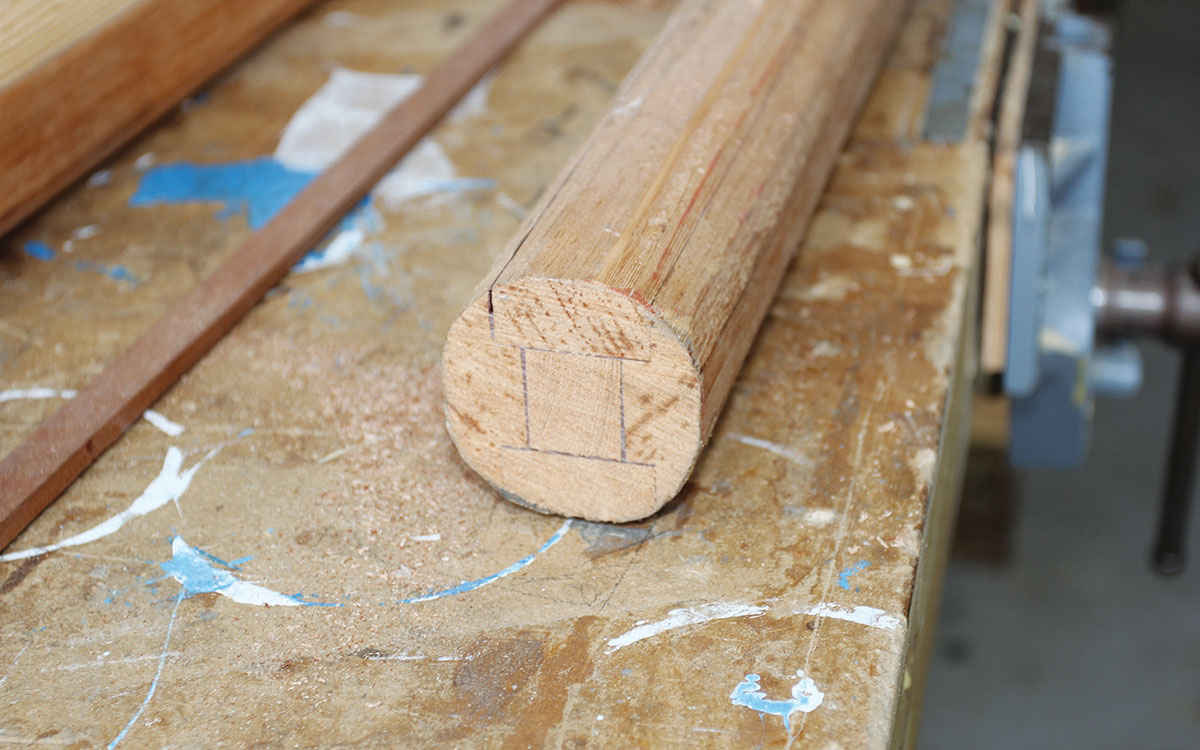
The boom has been planed into equal 16ths, and could be rounded (if required) with 32 sides planed by eye and a final sanding
Aileen – a Secret 20 on the River Dart
PBO reader Bill Thompson completed his own Secret 20, Aileen, about four years ago and has been avidly following the articles on the PBO build.
He wrote to us in response to our comments about how owners make their own alterations to customise or improve the boats:
“The cockpit seats have sensible coamings around the footwell which stands about 2cm up from the seat itself,” Bill explained.
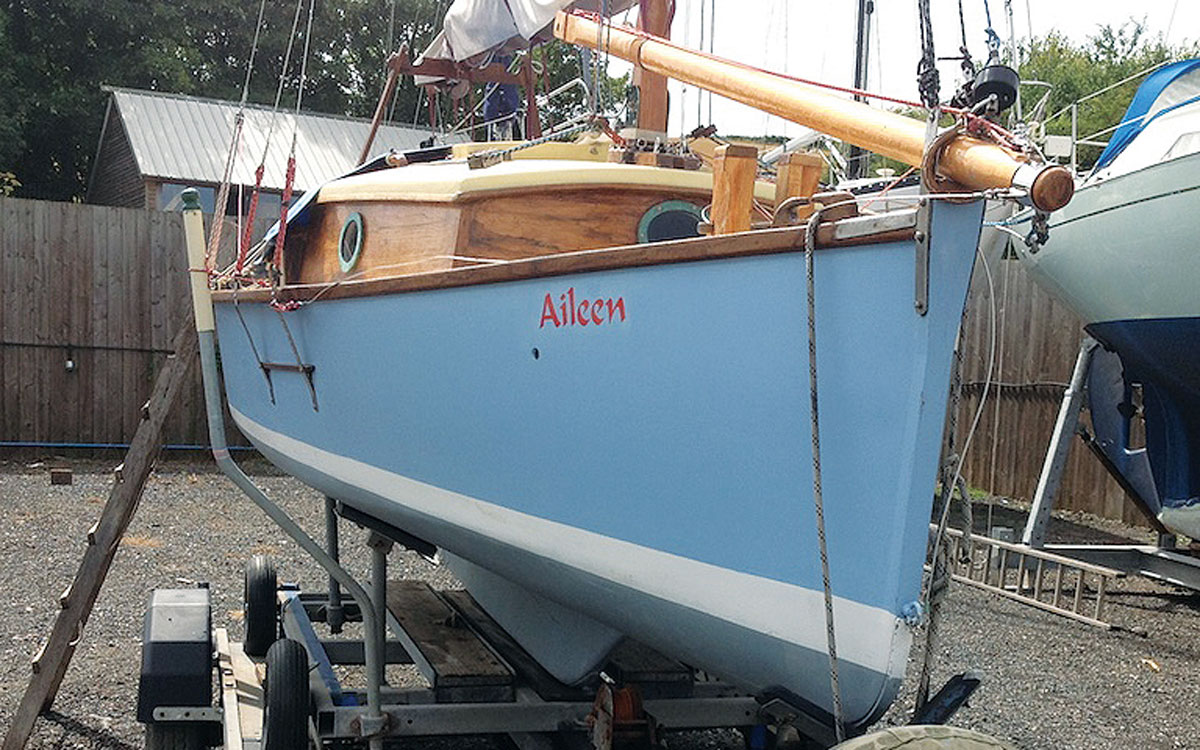
Aileen was completed in 2015
“But this retains a large shallow puddle either when it rains or on the odd occasion when I scoop some water into the cockpit. A drain spigot at the after outboard corner of each cockpit seat now sends this water into the footwell.
“The second point is a little less frivolous. The tabernacle sits on a pad on the cabintop beam and extends slightly forward of it. The cabintop is reinforced with light longitudinal battens between the transverse beams.
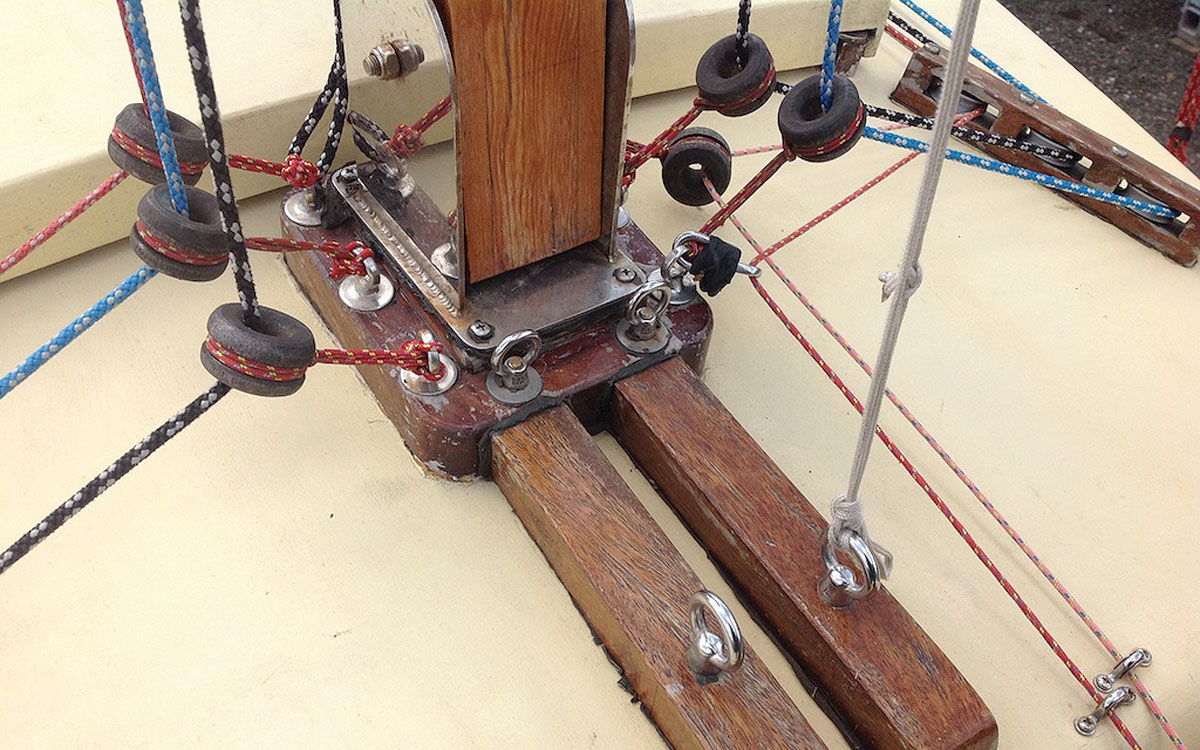
Bill Thomson reinforced her mast pad to spread the loads further after his first season of sailing
“In my first season I found that the centreline one forward of the mast had cracked downwards. I reinforced the mast pad with beams extending towards the bow to the forward cabin beam. I have had no further problem.
“These points do not detract from the fact that the design is fast, well balanced and fun to sail. It is also outstandingly pretty – in my own, biased view of course!”
Oarsome Chance
The Oarsome Chance charity offers school-excluded youngsters the opportunity to learn practical skills to build the confidence and attitude necessary to rejoin mainstream education. The children, both boys and girls aged between 9-19, haven’t had the best start in life, and often come from deprived areas with serious social issues.
Oarsome Chance offers them a practical alternative to channel their energy into something constructive, and in which they can be proud. With the social and practical skills they gain they are better equipped to re-engage with learning, and with Oarsome Chance’s support to ultimately find further training and potential employment.
The charity is always looking for volunteers, so if you can spare a few hours week, or can support the charity in other ways, they would love to hear from you. Visit oarsomechance.org or call the team on: 02392 504492