PBO’s project wooden kit boat receives more internal bulkheads and other load bearers. Jake Kavanagh reports
Designed in Australia and built by enthusiasts all over the world, the Secret 20 packs grace and pace into her streamlined hull. The kit is supplied as a series of pre-cut plywood panels, some pre-made parts such as the laminated roof beams – and lots of extra bits of high-quality timber with which to be creative.
Started by PBO’s in-house editorial team in 2016, the project has since been donated to the Gosport-based charity Oarsome Chance, where young people excluded from mainstream education learn practical and social skills necessary to re-engage with society.
After a flurry of activity on the boat, progress has slowed considerably since our last report, mainly because of the demands of teaching the students and the terrible spring/early summer weather the UK has endured to date. As such, Harvey – named in honour of a much-respected volunteer who died earlier this year – has spent much of her time in the boat shed.
However, a boatbuilding onslaught will ensue in the school holidays, when Harvey will have the team’s undivided attention. If all goes to plan, visitors to the Southampton Boat Show in September should be able to look at her up-close and chat with the Oarsome Chance team.
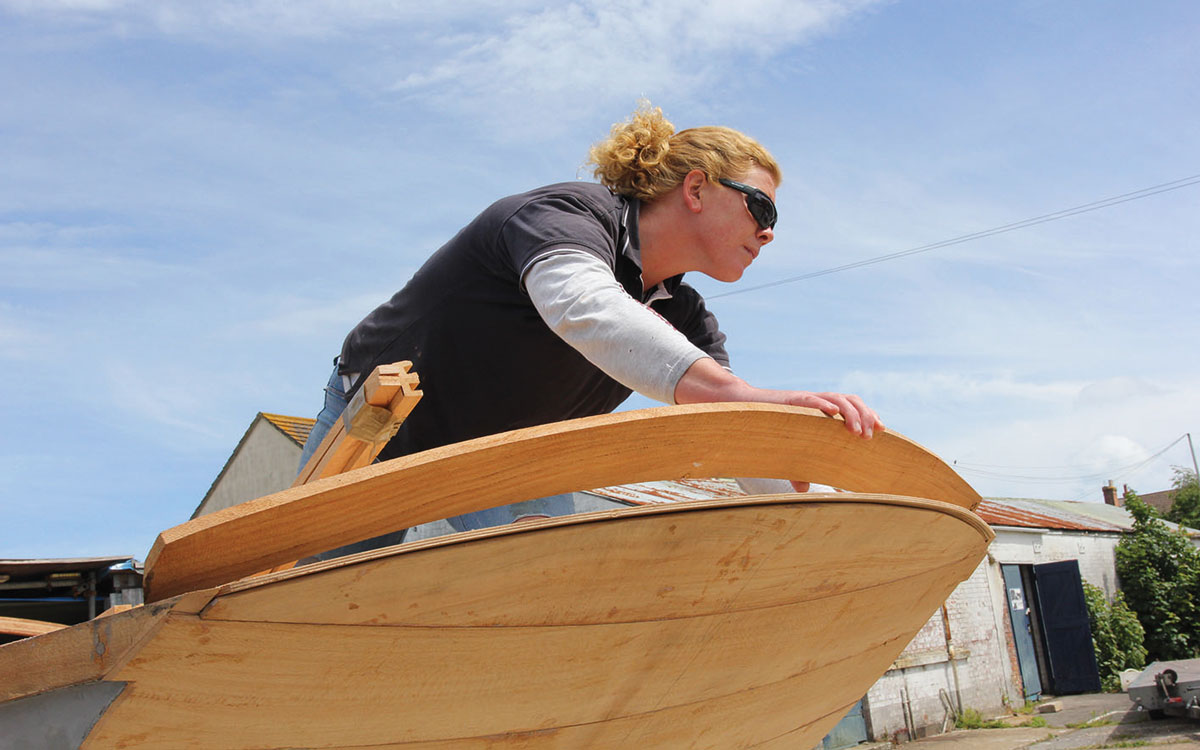
Team member Carly Seager offers up the mahogany trim that will define the outer edge of the rear deck
Bulkheads and beams
Heading up the boatbuilding team is Jon Carver, an experienced City & Guilds instructor and examiner. He works closely with Jesse Doyle, who qualified at the International Boatbuilding Training College (IBTC) in Lowestoft. Together, they have been putting their efforts into the decks and internal bulkheads that will support the curved roof.
“Jesse has been laminating the bulkheads,” Jon explained. “We’ve also been working on the corner posts for the coachroof. The cockpit coamings seem to come in at a different angle to what we expected, so we recently went up to Suffolk to see a completed boat.
Article continues below…
PBO project boat – the Secret 20 kit – is back in build
Like many boat projects Harvey, the PBO Secret 20, has been the victim of circumstance. This unique, classic-style performance weekender…
Project Boat update: Secret 20 completes deck fit-out stage
The Secret 20 is a beautifully designed classic sailing yacht that can be built from a kit, one of which…
“This gave us some great ideas as to how to finish that part of the build. Also, we saw some other innovations that we can incorporate to improve on an already very functional design.”
When we asked what the main challenges had been, Jon emphasised the need to ensure that everything was assembled in its exact place and ensuring the work is done in the correct order as when fixing with epoxy errors are difficult to rectify once it has cured.
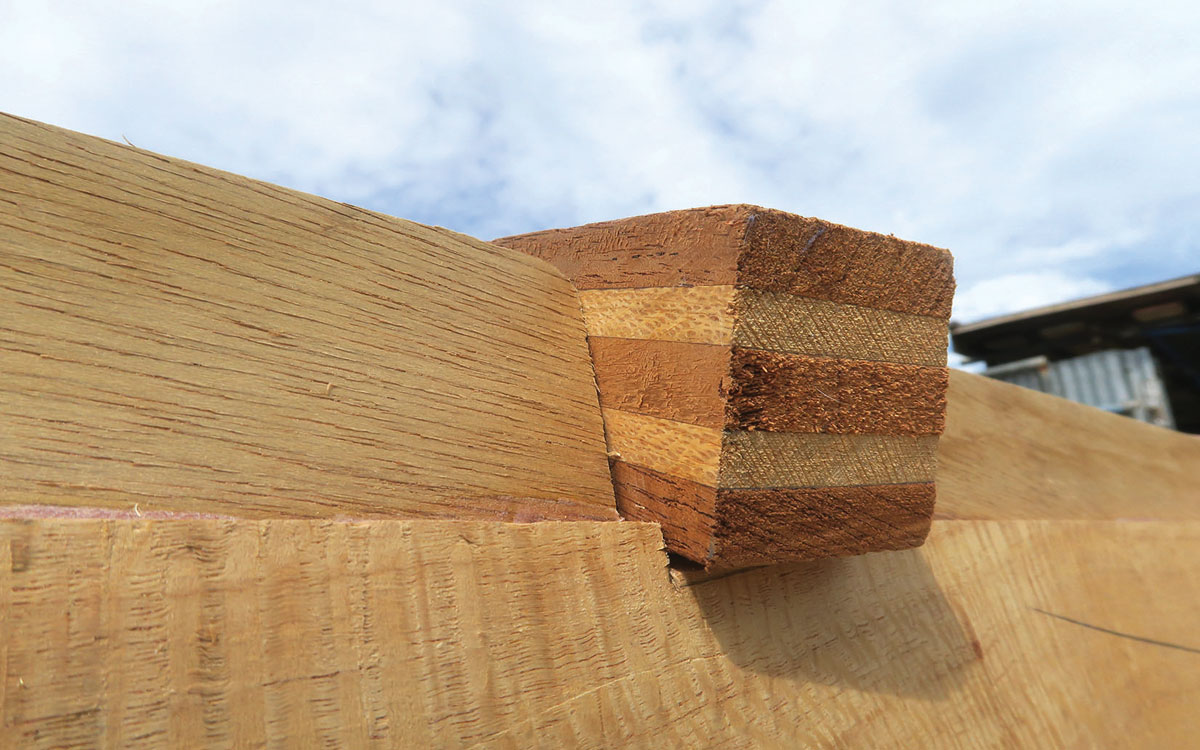
A detail of one of the laminated beams, and how it sits into a pre-cut slot in the cabin sides. The beams came pre-formed as part of the kit, although the Oarsome Chance team would have loved to have made them in-house. The process isn’t difficult but does require a jig
“There is a lot of dry fitting needed. It is sometimes easy to allow some things to slip back out of alignment, so it’s very important that everything is measured carefully so it fits into the right place. If one piece is set wrong, the error can cascade through the entire build.”
A problem currently being tackled is with an auxiliary forward deck beam which sits just inside the cabin to create a shallow shelf. “It should be about 100mm deep but ours has come out at around 160mm. This would’ve affected the position of the coach roof if unchecked.”
As the decks and floors go in, so do the side decks. These have been temporarily screwed into place to ensure a good fit – a ‘dry fit’ technique used widely in the boatbuilding industry. One superyacht yard for example, dry fits all the components into an engine room. The engineers ensure everything connects easily, then strip the whole lot out again for painting.
The same can be done on a small kit project like this. Temporarily make everything fit, then individually coat or paint the components outside the boat to solve access difficulties in the final fitout. The caveat here is that you shouldn’t pre-paint parts that you may want to use an epoxy fillet on when reassembling.
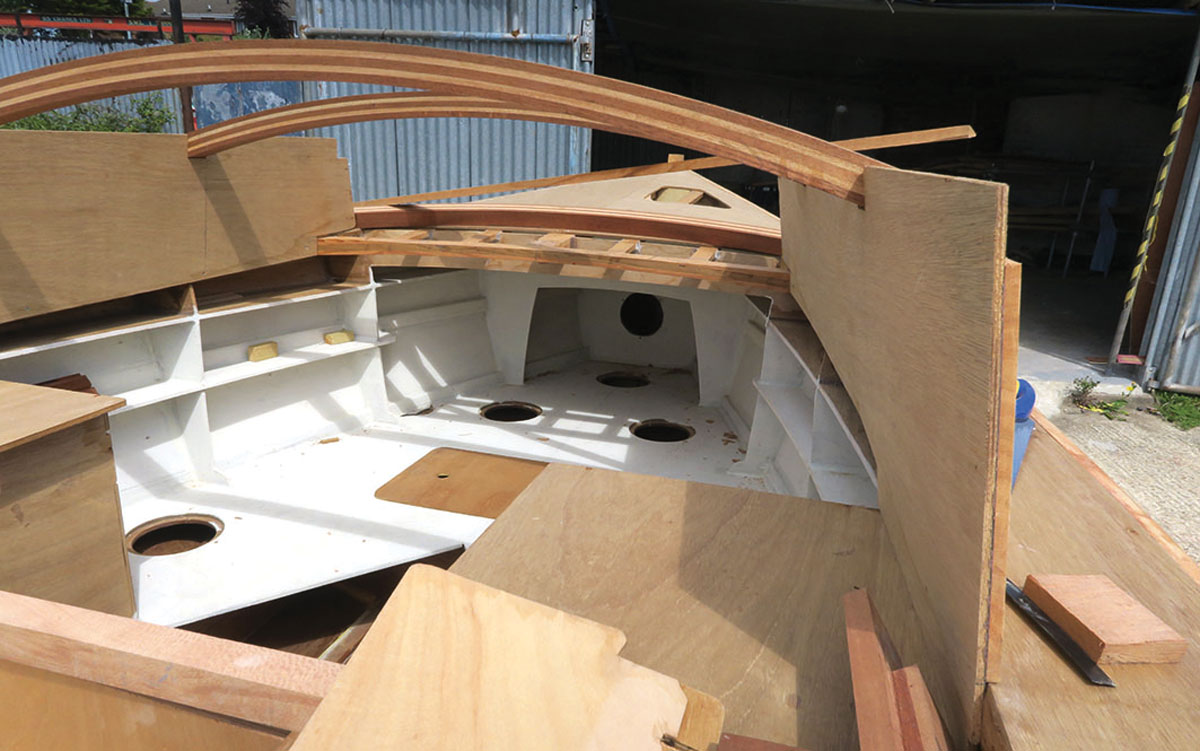
The forward shelf at the front of the cabin came in at a different width than expected, so the team have been working to compensate for the irregularity
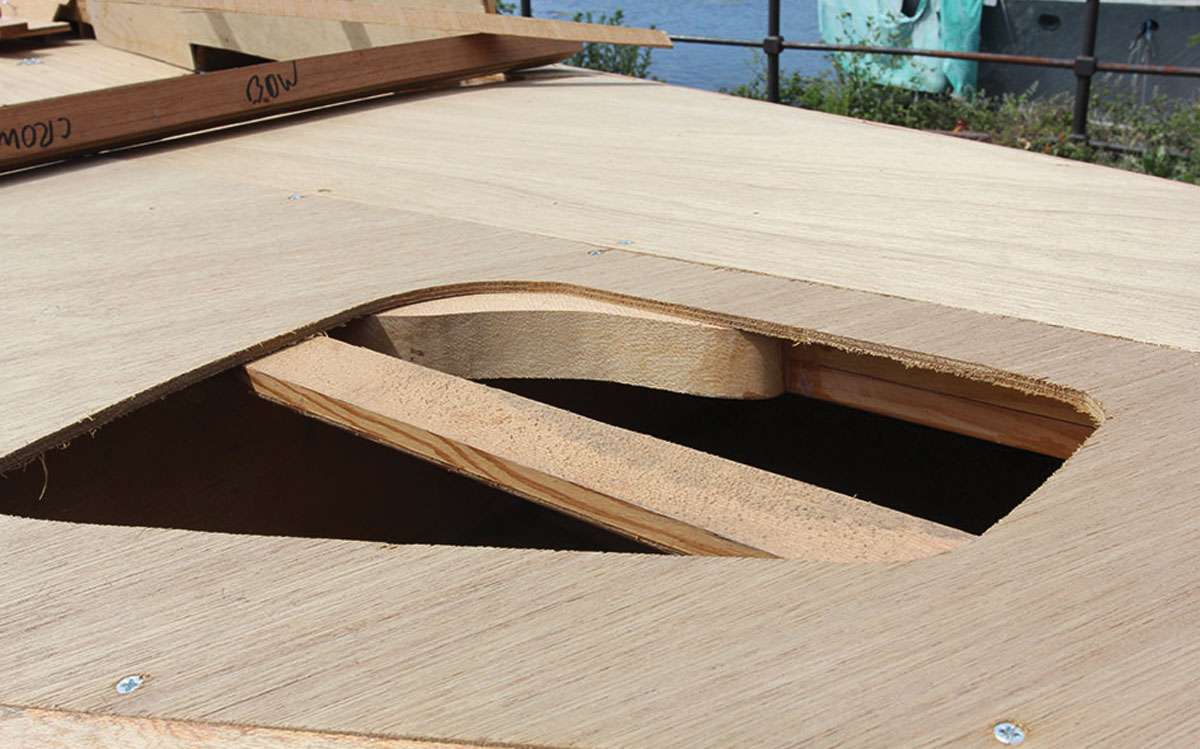
Forward hatch showing lodging knee for sampson post (fore and aft deck frame to be removed)
Getting trolleyed
A huge asset to any boatbuilding project is how the boat is supported in a cradle. Production builders often manufacture trolleys that are also rotating jigs. The hull can be inverted within a steel cage for work on both the underside and superstructure. In addition, the trolleys are often rolled into a raised deck or work station allowing full access around the decks.
At Oarsome Chance, a lower tech solution was used, but one that was still very versatile. “We built a trolley for the boat when we were working on the underside,” Jon Carver explained. “We really only needed something to help us move the boat in and out of the storage shed. The shed itself is a little restrictive so we prefer to work on Harvey outside wherever possible.”
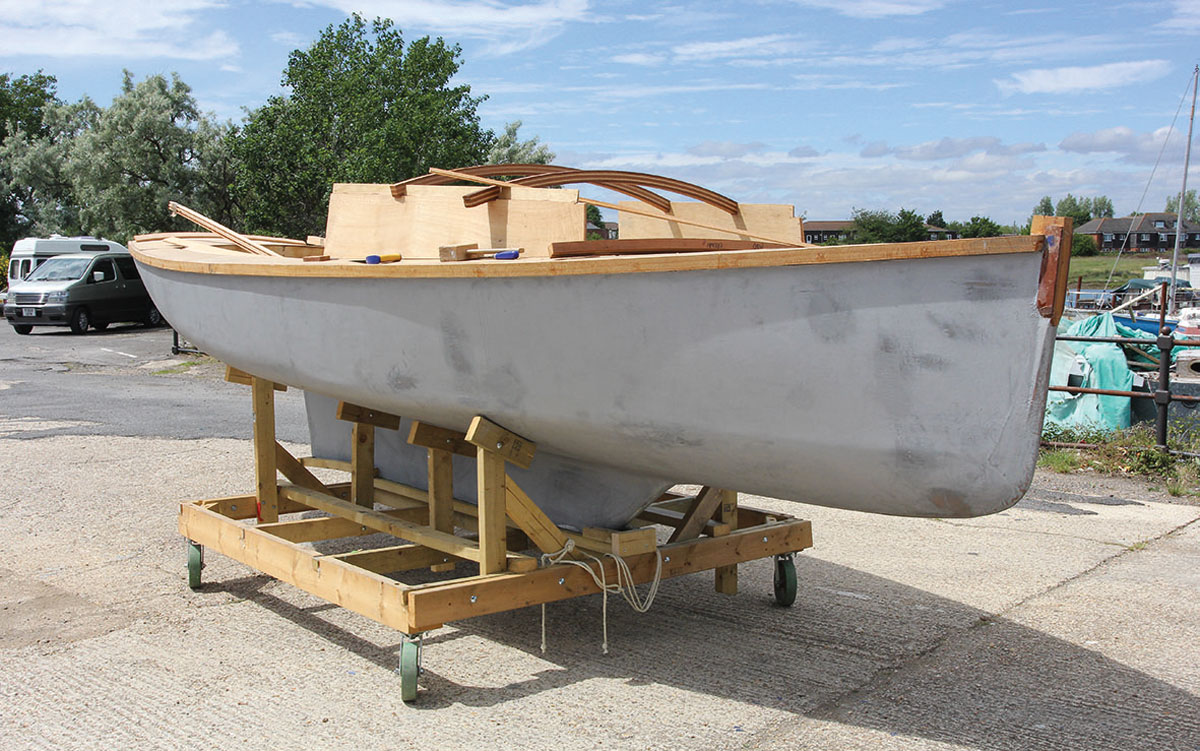
Harvey’s home-made trolley was assembled from ordinary builder’s construction pine
The trolley was made out of sections of rough cut pine. “We used what was lying around,” Jon explained. “We used 6x2in timbers on the sides, and 4x2in on the cross beams, but we have since doubled these up. The wheels are capable of supporting half-a-ton each, so there is plenty of spare capacity there.”
For projects that may sit in a cradle for a while, it’s a good idea to spread the load evenly across the hull to avoid any distortion. This is especially true with a cruising vessel that may be loaded with gear and fluids, as the uneven weight can cause a small amount of distortion if ashore too long – which is why yachts in cradles over winter will empty the chain locker contents off the boat and onto the ground.
Top secret news…
Regular readers may remember PBO Project Boat I – the restoration of Snapdragon 23 Hantu Biru – and may also have an inkling of what happens when we finish building… we usually give the boat away.
The difference this time is that Oarsome Chance intend to raise some much needed funding through a raffle or auction. The details are still to be finalised, but stay tuned if you want a chance of becoming Harvey’s new owner!
But why not keep her? Well, Oarsome Chance already has an impressive fleet of boats, including two RIBs, a Squib and the use of a Sweden 38 through a friend of the charity, but the most-used vessels are the kit-built rowing skiffs (hence the charity’s name) rather than sailing vessels.
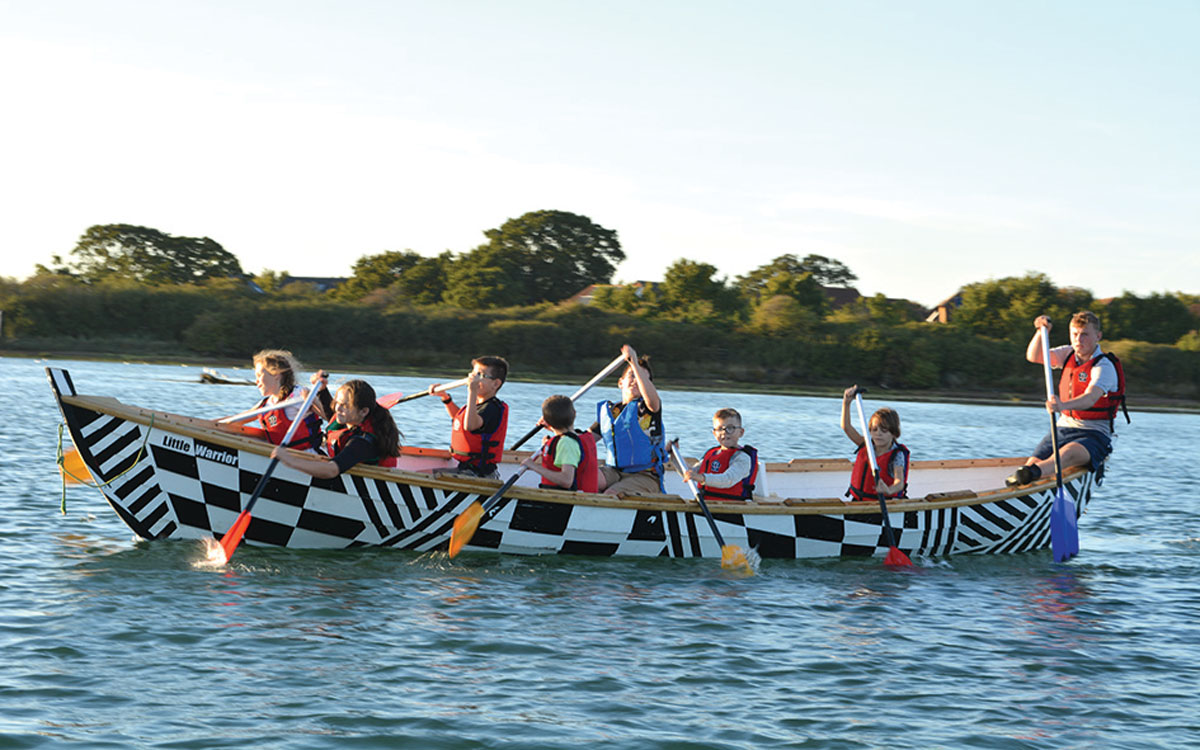
OC apprentice Luke Symonds at the stern of one of the charity’s rowing gigs with a group of school students. Photo: Jason Brodie-Brown
“We do a fair bit of sailing,” says charity principal John Gillard, “but rowing and powerboating is perhaps better suited to the kids we deal with. Wind awareness, booms clattering about their heads etc is a real challenge, whereas put a pair of oars in their hands… it’s a lot easier.”
The RCD and kit boats
Kit boats that are not manufactured to EU standards can only be put on the market five years after they have been completed. This means that Harvey will need to undergo EU Recreational Craft Directive (RCD) testing if she’s to be sold or even given away in the next five years.
We contacted CEProof, a Norfolk company that specialises in RCD testing. CEO Craig Morris has agreed to carry out the inspection, stability testing, which in this case would be a Pull-Over Wind Stiffness Test with the boat on the water, and certification.
Scruffie Marine, the Secret 20 kit manufacturer, is an Australian company – kits from EU manufacturers should automatically be RCD compliant once completed as long as the builder hasn’t altered the construction to any great extent.
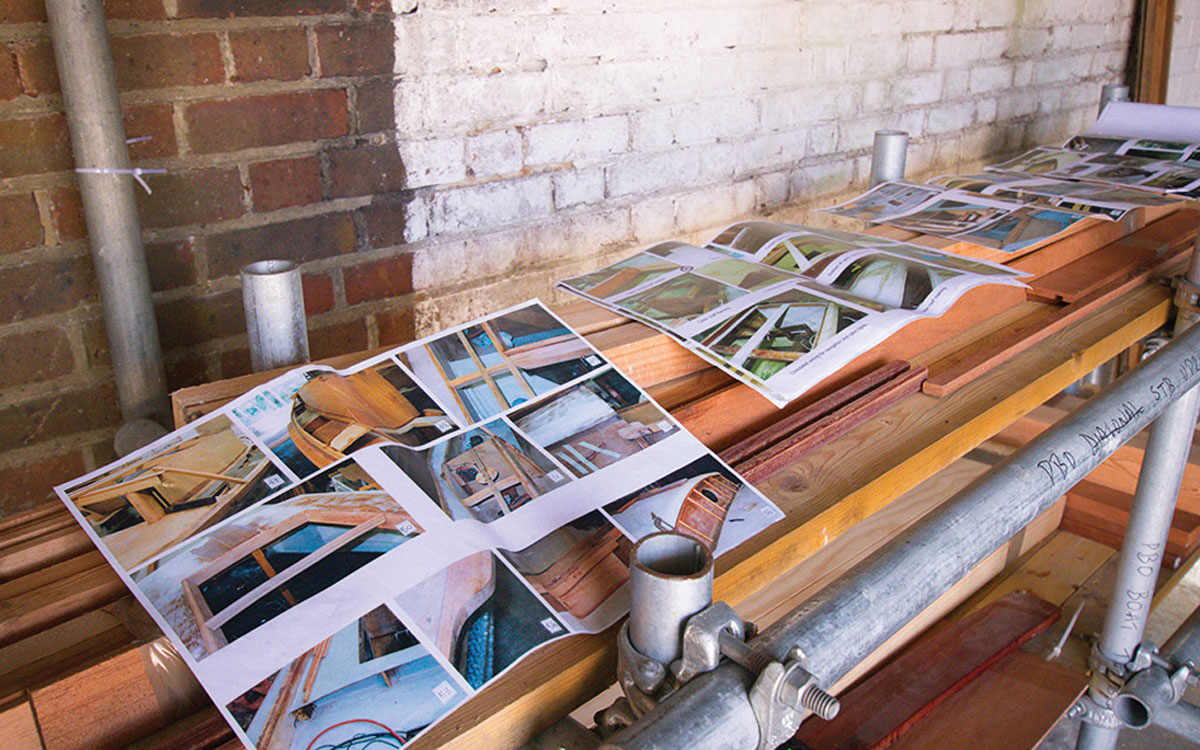
Photographs supplied by the designer help ensure everything has gone together where it should… Photo: Jason Brodie-Brown
The apprentices
Joe Swindale is one of two apprentices at Oarsome Chance. He works on various boat projects and also helps with activities for the school groups and specialist students that attend sessions with the charity. He works at the Gosport site twice a week and at the charity’s other site in Leigh Park, servicing bicycles, for the rest of the week. He prefers boats to bikes, he says.
“I was a naughty kid when I was at school,” says Joe. “I came straight from school to work here, so I’ve been here for two years. So I know how it is [for the students]. On Tuesdays we have a group of 15-16 year olds, so they’re near my own age – they don’t really listen to me. But the smaller kids do.”
In January this year, Joe began a four-year marine engineering course at Paragon training in Gosport. The course includes achieving RYA certificates for power and sail.
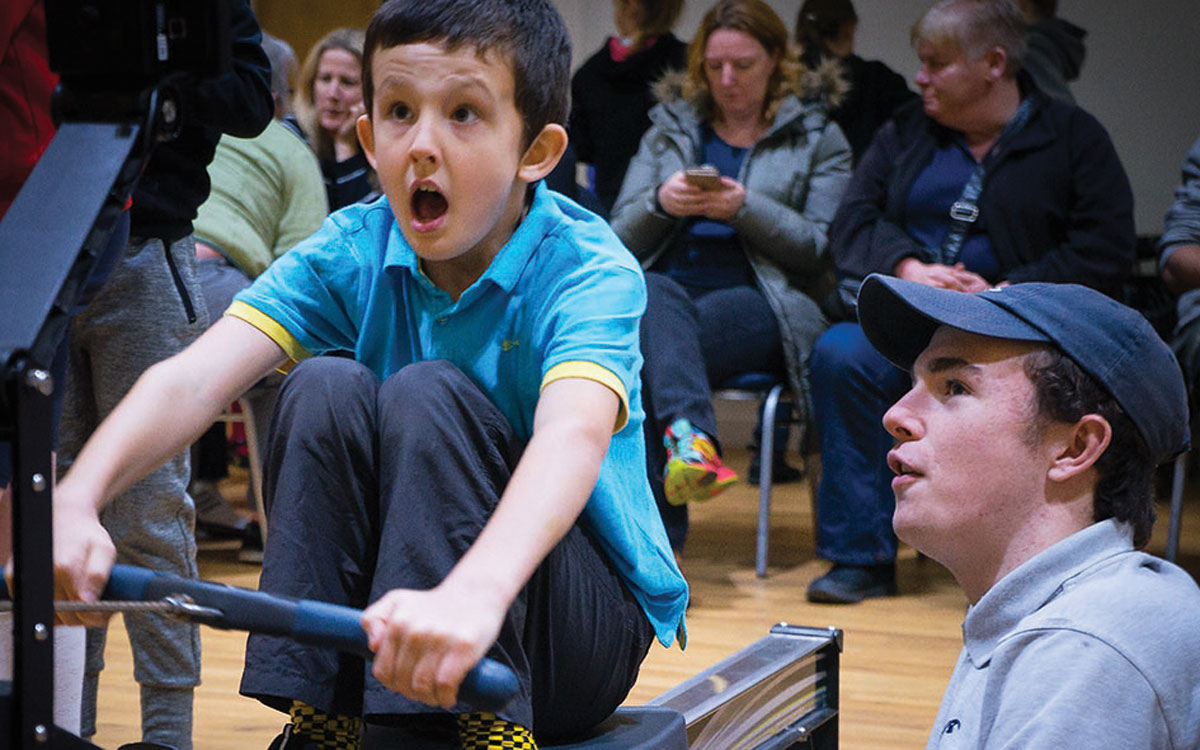
OC apprentice Joe Swindale coaches a young student with his rowing technique. Photo: Jason Brodie-Brown
Joe has his own squib, which he races regularly and has also been accepted to do the Tall Ships Race, taking part in a racing leg in July from Denmark to Norway, then cruising further north along the Norwegian coast before flying back.
Luke Symonds has been coming to OC for four years and is nearly finished his first year as an apprentice. Luke was thrown out of school for swearing at teachers, jumping over the gates, smashing windows and more at Charter Academy, Portsmouth.
“I was in trouble with the police through stupid things that I shouldn’t have done,” he says. “I started coming here on a Wednesday and a Saturday, just doing a few jobs with John – helping to repair the boats; helping to build the OC16 skiff, for example. Then finally, one day they turned around and said: ‘Do you want an apprenticeship?’
“I’m back doing maths and English again, so I regret messing around in school. I do a week per month at college then three weeks here.”
Oarsome success stories
Oarsome Chance is a unique educational/vocational experiment. Children who have been excluded from local schools are still required by law to receive education from the Local Authority.
Home schooling is rarely successful; special schools, such as the Harbour School, Portsmouth, have limited capacity and the private sector alternatives offering adequate staff-to-pupil ratios and specialist equipment and staff are hugely expensive (and profitable to their shareholders).
So vocational options, such as Oarsome Chance, meet an important need at about a third of the cost of the private sector and claim extraordinarily high retention rates.
“We started the whole thing as a route to employability,” says charity principal John Gillard, “which we are still very focussed on with our older students. But with the younger ones it really is to engage them back into society and then give them skills to build on long-term.”
There are currently 31 specialist students on the charity’s books, but the team also does watersports activities for mainstream schools (think groups of 60 schoolchildren building rafts and canoeing!).