Sailcloth has advanced a lot in the past decade. Here's a quick overview of the different sailcloths and types of sail construction you'll find on a yacht
Before speaking to your sailmaker, it’s worth knowing the different types of sailcloth on the market so you can understand which is best for your type of boat and sailing, and the pros and cons of different sail designs.
Woven polyester sailcloth
Though technology has advanced, the basic principles of weaving sailcloth haven’t changed since sailing began, with warp fibres (which run along the cloth) being bent around fill fibres (which run across the cloth).
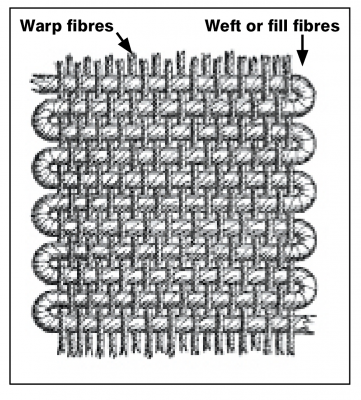
Warp and weft fibres of a woven sailcloth
The yarns have to snake over and under each other, and this is called ‘crimp’. When the cloth is loaded, these yarns straighten, resulting in stretch. Most woven sails are made from polyester (also called Dacron, a DuPont trade name) that was introduced by Bainbridge International as a replacement for cotton in the 1950s. Wovens are durable and economical, making them ideal for cruising sails.
Woven nylon – cruising chutes
Most spinnakers and cruising chutes are made from woven nylon because it has good tear strength. Nylons come in generic families ranging from 2.2oz down to 0.4oz, though these numbers do not directly relate to the cloth weight. Nylons can also be coated or impregnated and warp or fill orientated, but the important thing is the relationship between stretch, tear strength and weight. Heavier nylons do not always have lower stretch and better tear strength. A high quality light fabric can easily outperform heavy, low quality products.
Laminate sailcloth
Laminates are made by bonding together layers of different materials to form a sandwich. A simple laminate will consist of an open scrim of fibres with a layer of film bonded to each side. The film stops air blowing through the laminate while the load is taken by the scrim. Laminates are far more efficient than wovens as the scrim in laminates is ‘forced’ and not woven. The process bonds flat ribbons of fibre into a lattice. No weaving means no crimp and hence less stretch.
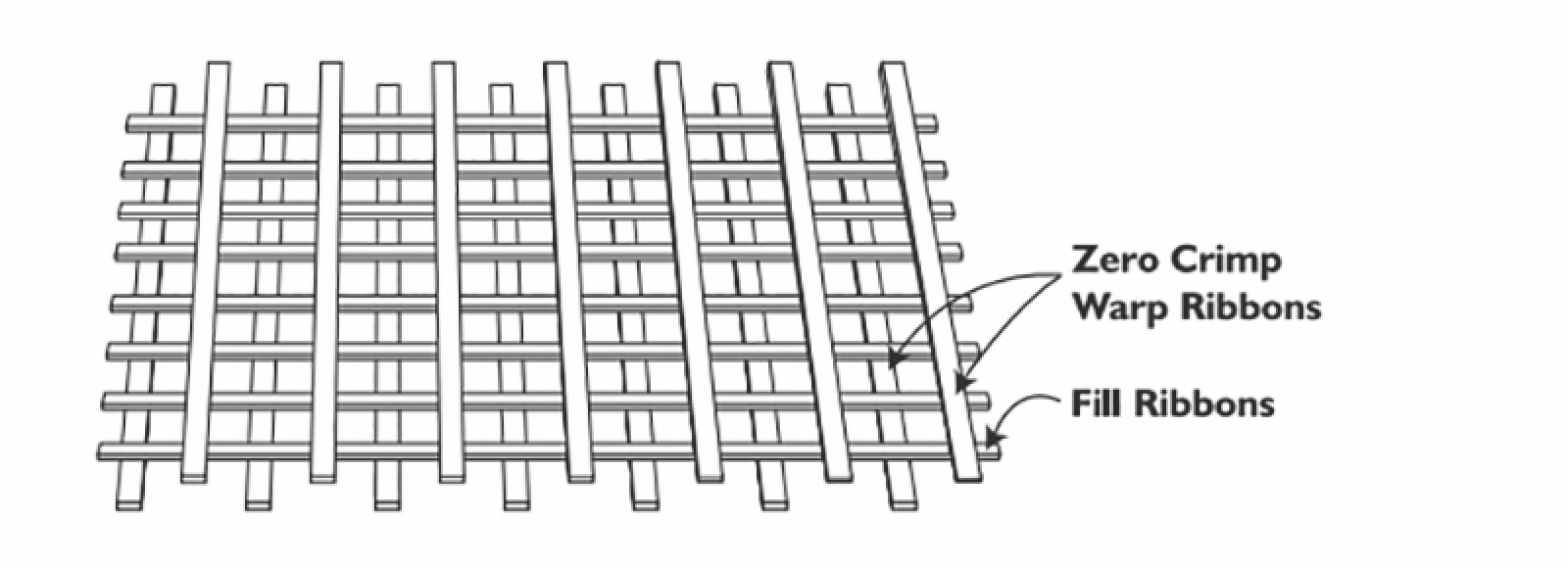
Scrim for laminates is bonded into a lattice
There are dozens of laminate products on the market, almost all of which contain three essential elements:
- One or more layers of film
- Fibres (such as Kevlar, Vectran, Spectra, carbon or polyester) that are laid into the laminate to enhance the strength in a particular direction.
- Taffeta (a woven fabric glued to the outside of the laminate).
One of the advantages of laminates is they’re much stronger for a given weight. A double taffeta cruise laminate might not be much lighter than the equivalent polyester but it will be much stronger resulting in far more stable shapes and better performance. Though stronger and better able to hold their shape, the downside to laminates (apart from cost) is that they’re not as durable.
Cruising laminate
Many people associate laminates with high-end race sails, but one of Bainbridge’s fastest growing markets is cruising laminates, a hybrid of woven and laminate. Based on race products, they are equally as strong, but have a light woven fabric bonded to both sides to give them durability.
Which cut?
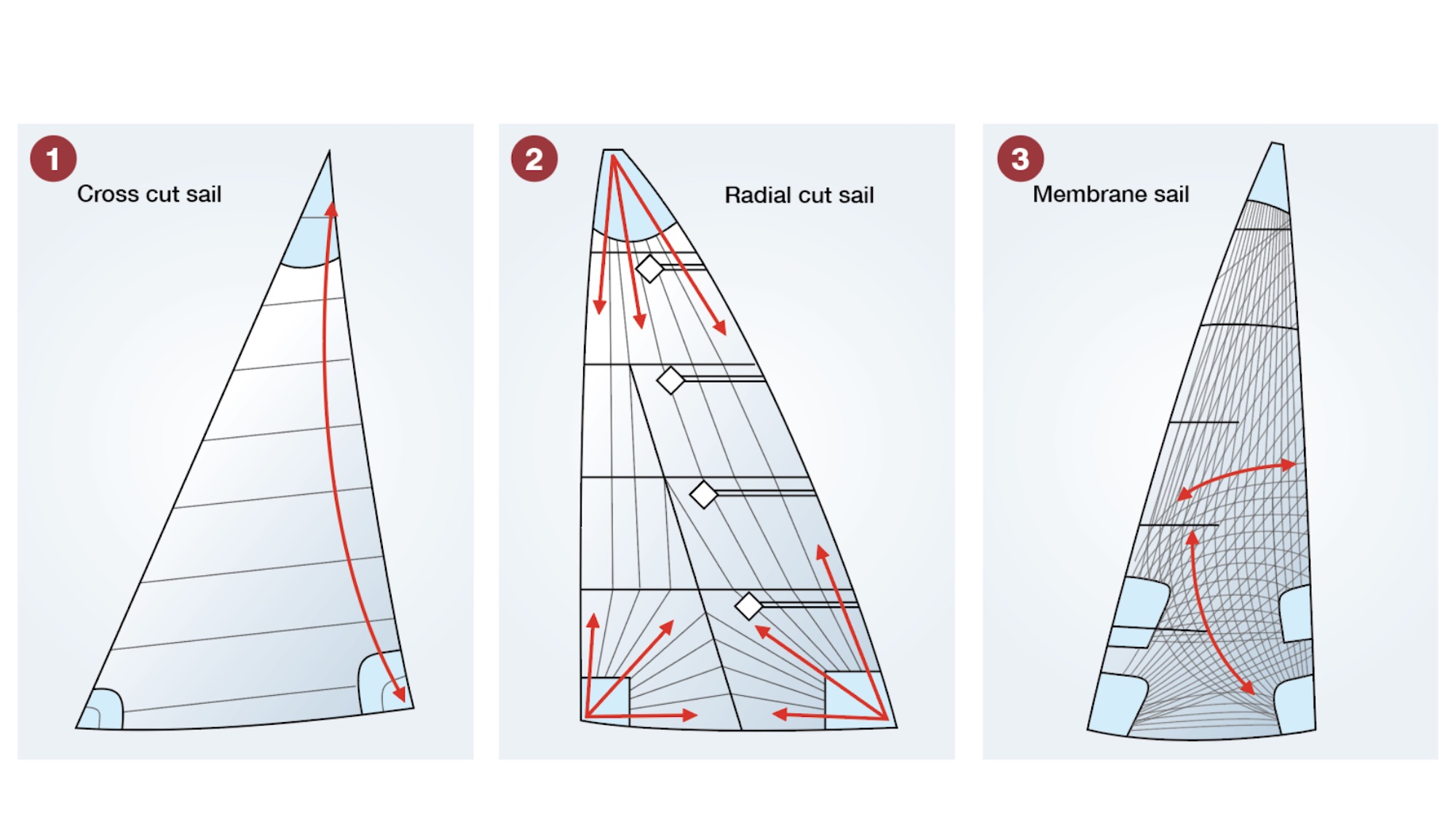
Examples of different types of sail construction
Crosscut sails
Crosscut sails are usually constructed from woven polyester panels of cloth that run horizontally across the sail. As fill fibres
ave less crimp, a woven cloth stretches less across its width than along its length. Bainbridge takes advantage of this by using larger (sometimes 400%) fill yarns than warp yarns.
Radial cut sails
Radial cut constructions more closely follow the load patterns on a given sail, with the loads mostly travelling along the length of the cloth. They’re usually made from laminated sailcloth – that is, any fabric consisting of two or more layers adhered together. Radial cut fabrics are much stronger in the warp direction than the fill, which means they can be used in a different way. The panels can be cut in long, narrow triangles and trapezoids
with the strong warp fibres aligned with the loads in the sail that radiate out from the corners.
Membrane sails
The most advanced sail construction type is a membrane sail, which is custom-made. Individual panels are constructed on a table with the fibres being arranged with the boat owner’s usage in mind. Once complete, another layer of film is added, the air gets sucked out and the whole lot gets pressed and heated so you end up with a custom panel.
Individual panels are then glued together to make up the complete sail, with the seams being stronger than the laminate itself. This more complex solution for load distribution means better performance.
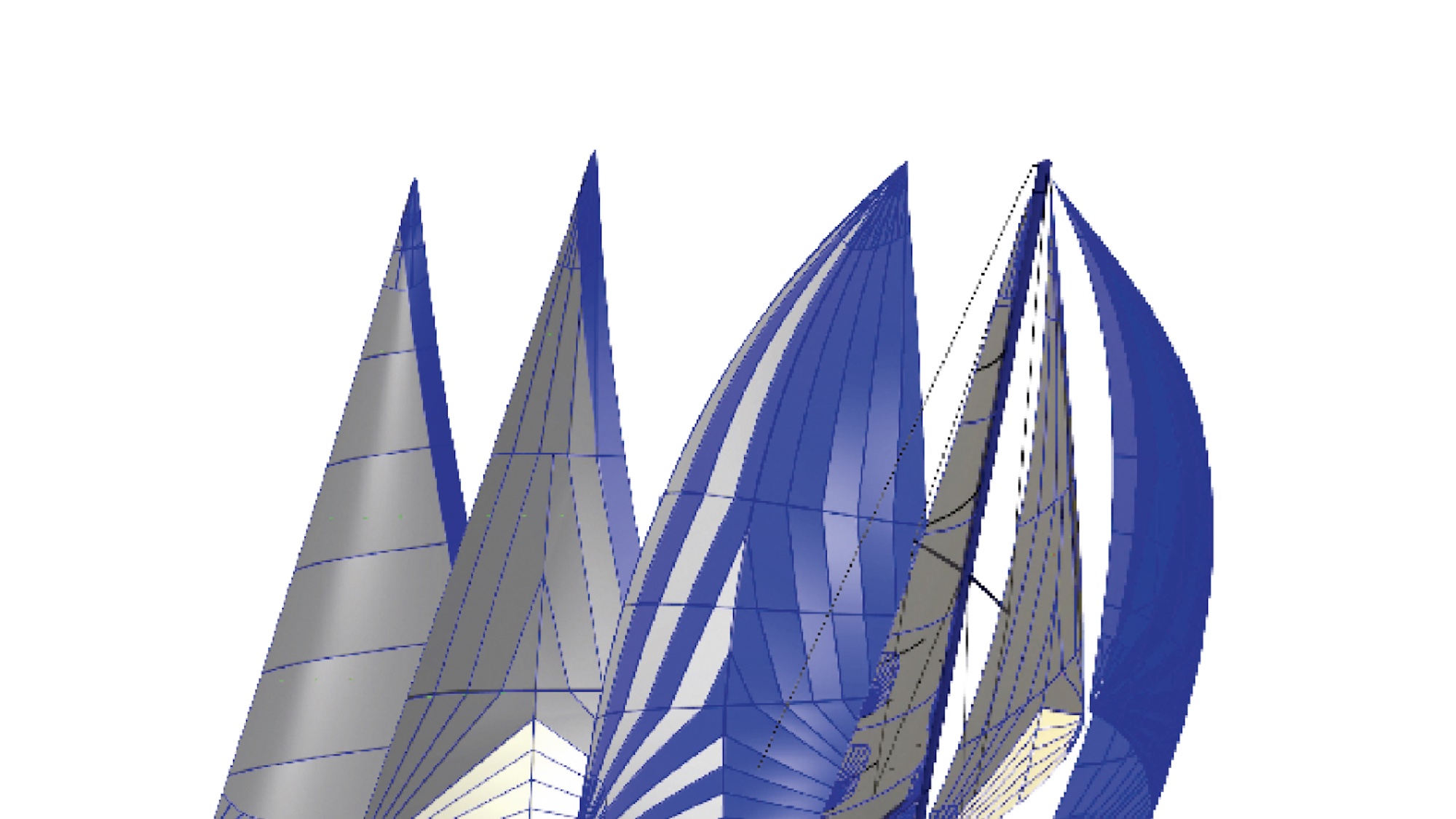
Computer images of crosscut sail, radial cut sail, cruising chute and all three on the PBO Project Boat, a Maxi 84
Understanding bias
The sailmaker will know how the loads in your sail radiate out from the corners, but with so many variables, not all loads will exactly follow the yarns, meaning some of the stress is ‘off threadline’.
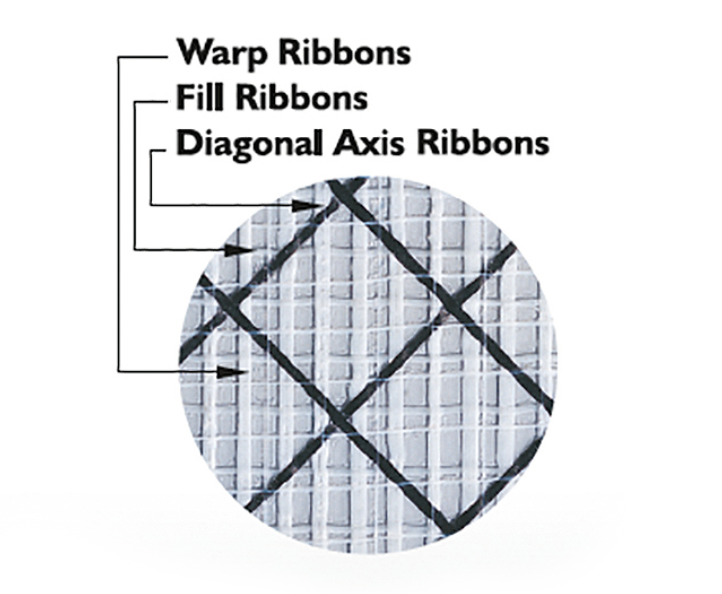
This DIAX laminate cloth by Bainbridge has a diagonal scrim
To reduce this, Bainbridge try to minimise bias (diagonal stretch) in woven cloth by locking the warp and fill yarns together by impregnating with a resin to chemically bond them together.