The results of a Royal Yachting Association (RYA) survey to investigate the causes of kill cord and kill switch failure and the results have been published.
Some 1,016 respondents from 23 countries, including the Falkland Islands to the USA, the Philippines and Australia, took part in the survey, although 90% were from the UK.
The over-whelming majority of respondents stated that they had never experienced a kill cord or kill switch failure, however a third described experiencing a failure of either the kill cord, kill switch or both, with problems occurring across the board in terms of engine size (sub-4hp to 150+hp) and with 73% of problems reportedly occurring in engines aged 2-10 years.
The survey found:
· More than 65% of respondents kept the kill cord ashore or in a locker on the boat, however, almost 30% of respondents indicated leaving the kill cord attached to the kill switch when not in use. This could potentially lead to a number of issues, such as UV and salt degradation or potentially fatiguing the kill switch spring mechanism possibly reducing its effectiveness.
· More than half of respondents got their engines serviced by the local service dealer for the engine, while just under 75% of engine users were undertaking periodic maintenance checks, similar to those that you’d do prior to a long car journey. However, there were a handful of Powerboat Instructors, safety boat crew and recreational powerboaters who were either undertaking no checks, or were unsure whether any were being done.
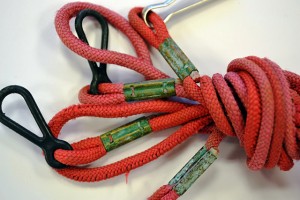
Corrosion on crimp
The reasons given for kill cord failure point to the need for closer inspections being carried out before usage to identify weakening of this vital piece of equipment:
· Kill cord came apart because of rusty metal components – crimp or clip
· Kill cord snapped with no inner cord
· Kill cord lost elasticity and stretched, so difficult to keep on leg without it dropping to the floor and falling off or activating the kill switch every time the helm moves their feet
· Kill cord outer cord perished and just left inner core exposed
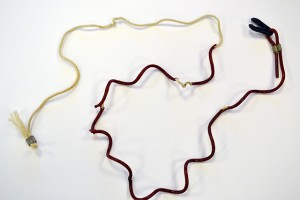
Fatigued and perished outer core
There were also problems with non OEM (Original equipment manufacturer), aka after-market kill cords which are often easily available and cheaper than OEM kill cords. Problems associated with these were that the attachment jammed in the switch as it was too tight fitting, or that they were too loose in the switch mechanism and therefore did not reliably pull the mechanism apart enough to activate it.
A further area where failures occurred were through operator error:
· Kill cord was not properly attached
· Kill cord slipped off the wrist or continually pulled out of the kill switch when worn around the wrist and pull-starting
· Expecting the kill cord to disconnect by walking around the side of the console (this would cause too much friction and the kill cord may not disconnect).
The survey also found that 66% of kill switch failures failed with the engine not stopping, the rest were that the engine wouldn’t start. When asked what the helm was doing when the failure occurred, it was heartening to read that 30% were testing the kill cord/switch at the time.
Rachel Andrews, RYA chief instructor, motor cruising and power said: ‘It was great to receive such a wide spread of respondents from all boating backgrounds with the three biggest sectors being, RYA dinghy/windsurfing or powerboating instructors, recreational powerboaters and RYA recognised training centre principals or chief instructors.
‘It has long been in the RYA Powerboat Level 2 syllabus to test the kill cord before setting off, and it is great to see that not only is this practice embedded, but that it is picking up issues early before an emergency situation occurs.’
While 12% of respondents noted that they were attempting to stop the engine when the kill switch failed, but it is unclear from the responses whether they were testing the kill cord or whether they genuinely needed to stop the engine.
Rachel added: ‘The results of the survey show that the good practice of testing a kill cord before setting off is fairly widespread and it is important that this habit continues to be emphasised on courses.
‘However, it also showed that there are areas for improvement in maintaining equipment, such as checking kill cords for signs of fatigue, discolouration, stiffening, loss of elasticity and any metal or plastic clips; and checking the actual kill switch.
‘The data we have captured can now be used to inform the general public and guide the RYA when reviewing training syllabi in the future and may also be used to help shape future research.’
For more information about kill cords visit www.rya.org.uk