PBO reader Kirk Forrest has a question about corrosion protection. Marine surveyor Colin Brown has this advice...
Bob Williams writes: “During a recent chat at my sailing club questions were discussed about anodes, galvanic corrosion and earthing, sailing in salt water and then into fresh water. As expected, there were many different views and disagreements.
“What are the best methods to protect a vessel going from one water type to another and what earthing methods would you recommend?
“Could a lightning conductor, as used on tall buildings be of use, either the rod type or the flat plastic-covered type that can be bent to follow the contours and shape of a vessel? Would it also protect against galvanic corrosion?”
PBO corrosion expert Colin Brown replies: “It would be easiest to answer your questions with a quick summary of the hows and whys of anodes. If you connect any two different metals and put them in salt water, they’ll create a small but measurable voltage.
“This can drive electrons from one metal to the other so one metal corrodes preferentially leaving the other metal undamaged. Metals can be arranged in a hierarchy of potential – a Galvanic Table. Metals low down the table are suitable as anodes and those higher on the table will be the cathode.
Article continues below…
Boat anode protection: How much do I need to prevent corrosion?
PBO reader Arthur Gilbert asks: “Is it necessary, and if so where, to fit anodes on my recently acquired Leisure…
How to: check and change an anode
Galvanic corrosion is a phenomenon that affects the majority of boats. If you have two dissimilar metals, such as stainless…
“The bigger the difference, the stronger the reaction. In our context the anode might be zinc, aluminium or magnesium and the cathode you want to protect might be a manganese bronze propeller or a stainless steel shaft. This process is known as galvanic corrosion.
“The corrosion is driven by the natural potential differences between metals and tends to be a slow process. Electrolytic corrosion takes place where there is an external source of electricity such as a stray current from an electrical fault and this tends to be a more rapid process depending on the voltage available.
“Neither of these are the same as electrolysis which is a process that uses electricity to break or separate compounds or solutions – not really an issue we have to consider here.
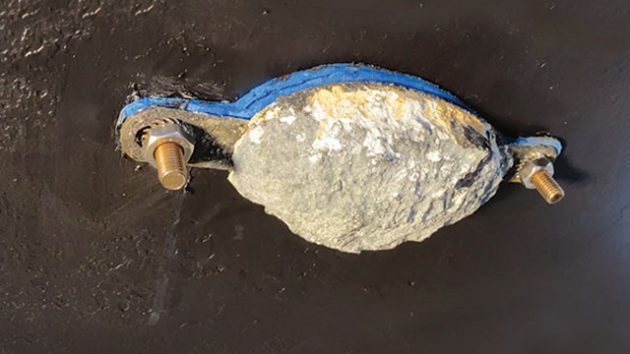
This anode has done its job and is now severely depleted so needs changing
“For this natural circuit to work on a boat the two metals have to be electrically connected by a conducting wire or a conductive hull material and both have to be immersed in an electrolyte. No connection, no protection.
“We’ve traditionally used zinc as an anode for vessels in salt water, aluminium in brackish water and magnesium in fresh water. As salt content falls so does conductivity and so the anode and cathode materials have to have a larger voltage difference on the galvanic scale to maintain protection.
“If a boat regularly sees short-term changes in salinity such as marina or river to sea and back then the best anode choice would be aluminium. Aluminium is cheaper than zinc and has a higher amp-hour per kilogram rate than zinc so the anodes tend to last longer.
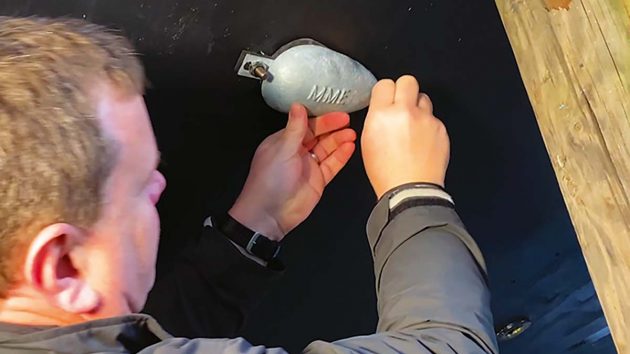
Installing a new anode
“Most of us who sail in UK coastal water will regularly be in areas of lower salinity so aluminium seems like the best choice for the majority. If you’re changing water type for more than two weeks then you should change anodes to maintain protection. This might be the case if you were going into fresh water like a canal or locked river basin.
“Zinc is fine if you stay in full salinity water but zinc anodes immersed in fresh or brackish water grow an oxide crust that can insulate the anode and prevent it from working even after returning to salt water. It’s hard to remove the crust and the use of a wire brush can contaminate the anode and further reduce its function.
“One tradition was to electrically bond all through-hull fittings together with wire to keep them at the same potential and connected to an anode. I’m not convinced this has any merit partly because an anode has a short range of influence and has to be able to ‘see’ the cathode.
“I doubt that the inside of a hose tail where the metal is thinnest will ever be in range so it pays to fit good quality components made of naturally corrosion-resistant metals and leave them galvanically isolated.
“Another issue with electrically bonded components is that in the event of a stray current fault, all through-hull components are automatically part of the problem with the possibility of rapid corrosion driven by the full battery voltage.
“Lightning conductors tend to be made of copper which conducts well but is too noble to be of any use as an anode in all common marine applications so would not be of any benefit in trying to avoid corrosion.
“A small piece of copper conductor strap could be useful to bridge a flexible coupling between the gearbox output flange and the propeller shaft.”
Got a question? Email pbo@futurenet.com and we’ll put it to our panel of experts.
Why not subscribe today?
This feature appeared in the January 2024 edition of Practical Boat Owner. For more articles like this, including DIY, money-saving advice, great boat projects, expert tips and ways to improve your boat’s performance, take out a magazine subscription to Britain’s best-selling boating magazine.
Subscribe, or make a gift for someone else, and you’ll always save at least 30% compared to newsstand prices.
See the latest PBO subscription deals on magazinesdirect.com