Jake Frith undertakes a sea trial aboard the innovative SEAir Flying Tender 80 foiling RIB and wonders whether all small motorboats will soon be flying on foils…
Having sampled a prototype version of this French foiling RIB three years ago, I had to reluctantly admit it wasn’t quite there yet.
It had, and still has, roughly L-shaped main foils about level with the front of the console, and in the early version I tried these had the habit of suddenly losing lift, usually only on one side.
It’s hard to explain exactly how disconcerting this feels, but a forward tipping and decelerating motion is not something you want to feel at over 30 knots in a choppy Solent.
The difference now with the SEAir is in the work that has gone into the foils and control system, and the test of this first production version confirmed these improvements with us foiling whenever we wanted and not making a single unplanned drop off foil even with numerous wakes and a short chop to contend with.
You begin to feel the foils are ‘doing something’ at about 10 knots, with full foiling achieved at about 16 knots. It’s best to stay out of the 10-16 knot range though, because the foil control system has to increase the foils’ angle of attack to keep the boat flying and this is not the most efficient way to travel.
Article continues below…
RS Pulse 63 test drive review: Could this electric RIB change the world?
When RS Sailing, the world’s largest manufacturer of sailing dinghies, announced a few years ago that it would be building…
2022 Southampton Boat Show: Insights into the sail and power market
Peter Poland discusses interesting new boats at the Southampton International Boat Show (SIBS) and the state of the sail and…
It’s the front foils that do most of the lifting and all of the balancing on the SEAir, and managing them is a matter of a single button push to tell the computer to take over, tweaking the foils about six times a second to keep the boat in the air.
The rear foil is a smaller, swept wing affair that slips over the gearbox of the outboard motor. It only adjusts its angle of attack as far as the engine’s trim and tilt change it so it’s not part of the ‘on the fly’ pitch control system.
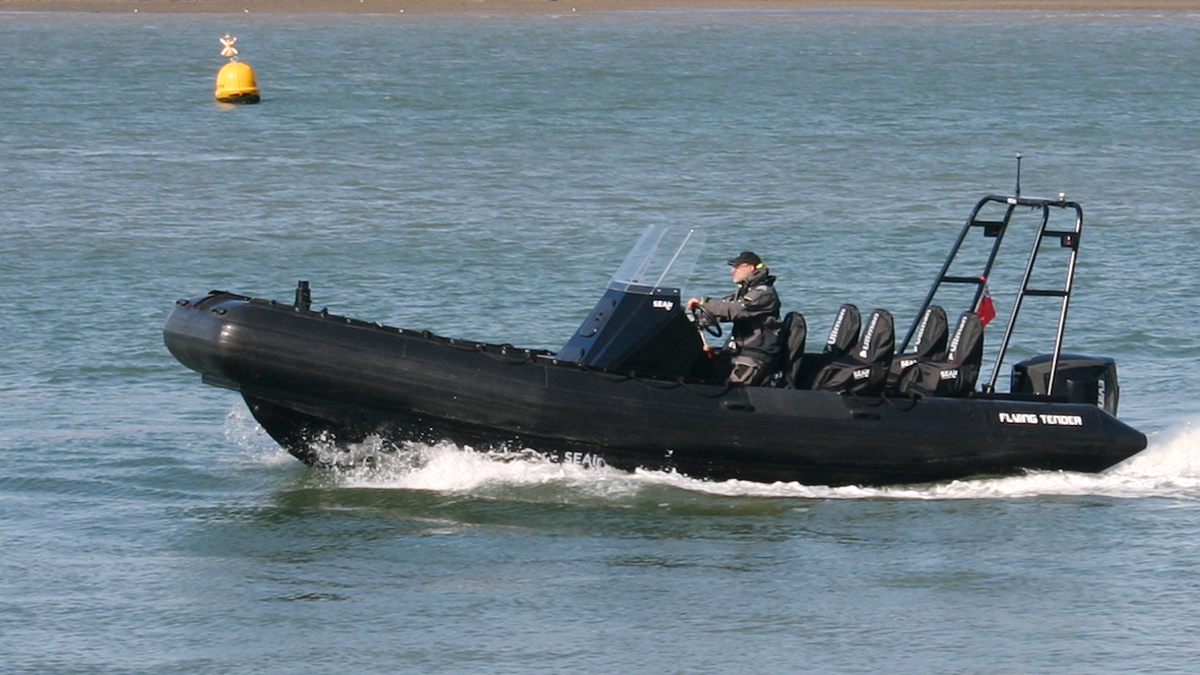
At about 10 knots she starts to give a sensation of lifting
Why bother with foiling?
So why bother putting a RIB on foils? Simply, the pressures to reduce energy consumption demand considerable hull efficiency gains, and hydrofoiling is one way of achieving them. Most of a boat’s drag is split into skin friction and wavemaking drag.
Unusually for naval architecture, these are two fairly self-explanatory terms. A well-designed hydrofoil reduces both of these sources of drag in comparison with a conventional planing deep vee hull.
It reduces skin friction because this is dictated by the surface area of hull, or foils that are in contact with the water. Wavemaking drag on the other hand is caused mainly by the interaction of a boat’s hull with the surface, and clearly a hydrofoil only interacts with the surface to the extent of the thin foil verticals that support the foil.
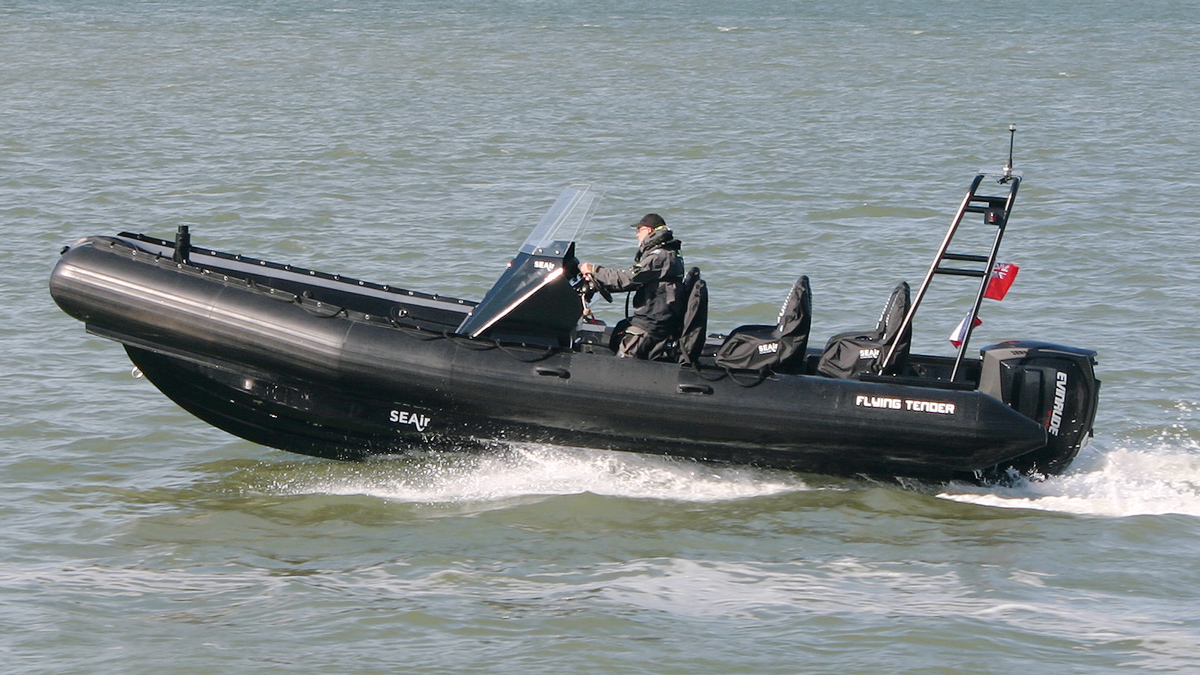
Between 10-16 knots she’s semi-foiling but the foils and servos are doing a lot of work
Hydrofoils do create waves, both from their support masts and the foils themselves, but these are smaller, lower energy waves than a traditional wake, hence the efficiency gain.
SEAir claims between a 20% and 35% fuel saving over a similar boat, but that’s not the end of the story. Whole body vibration is also a key concern for commercial vessel operators, and SEAir is aiming the Flying RIB at commercial and military operators to start with. The French Navy’s special forces are an early adopter.
The idea is that slamming is reduced when you fly above the surface of the water, and while wave tops can be felt hitting the hull, the boat did seem to be avoiding the tendency that some RIBs have of reacting to a series of waves as an ever-increasing series of oscillating impacts.
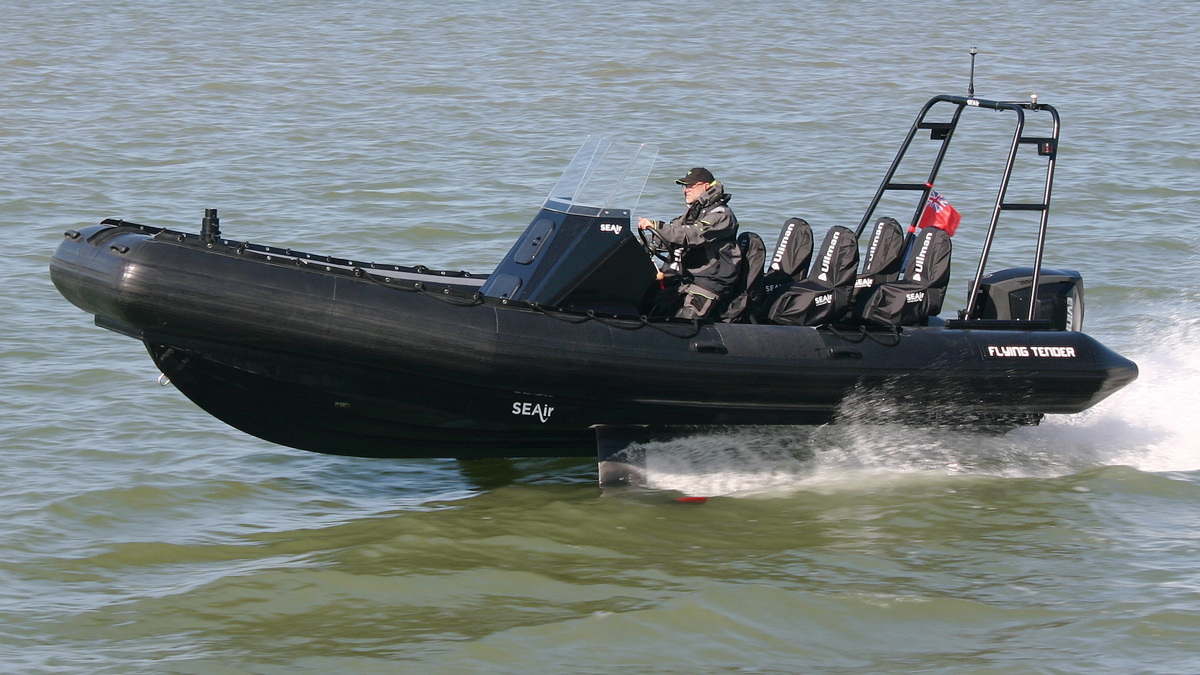
Fully foiling above 16 knots is where the boat’s true benefits are found
However, I did note the test boat was equipped with a full set of Ulman suspension seats, suggesting that hydrofoiling doesn’t do away with shock impact from the sea entirely.
Powered flight
OK, I can hear all seasoned readers sing in chorus: ‘Hydrofoils have been around for 100 years – this is nothing new!’ The thing about hydrofoils, though, and especially small ones, is balancing the forces to achieve pitch and roll stability in choppy water.
It’s really only the improvements to composites and waterproof computing power that have made it practical to build a production foiling RIB of this size.
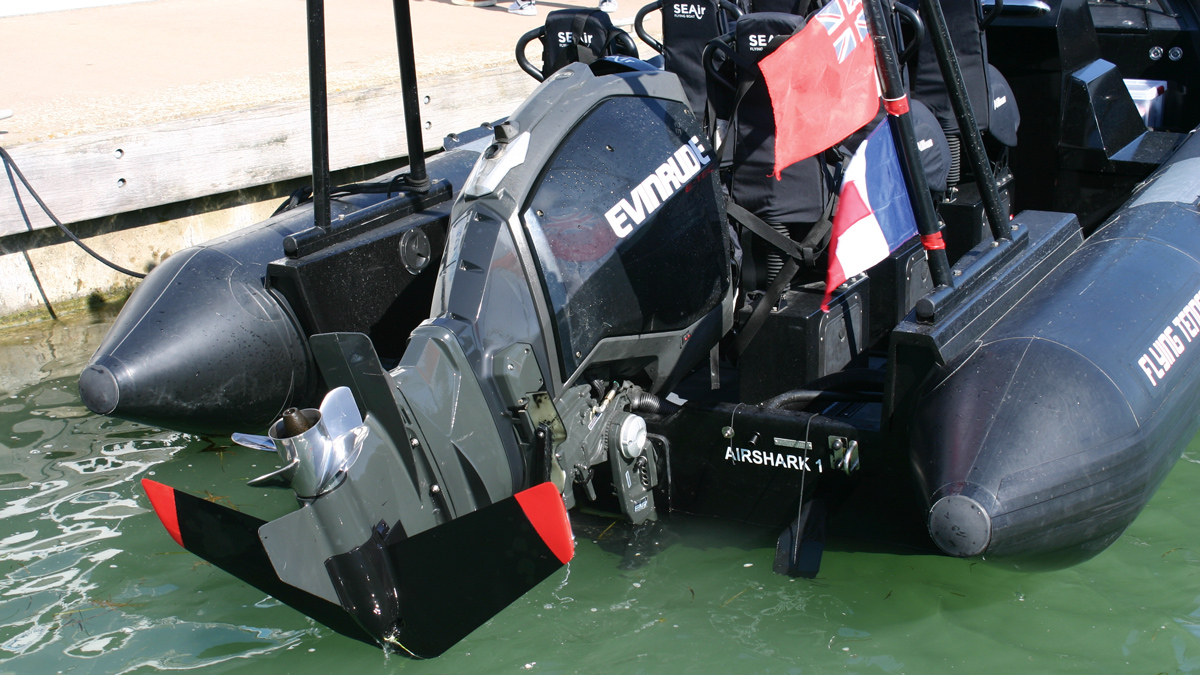
The aft foil slips over the front of the gearbox
A hydrofoil designer will tell you that designing an efficient small hydrofoil craft is in many ways harder than cracking powered flight was back in 1903. A hydrofoil boat has to be stable in displacement, planing and foiling modes, and they all require several very head-hurty pages of maths.
There’s also a necessity to pare back drag when the boat is somewhere in the grey areas between those three modes.
There are a few other hydrofoil motorboats out there, but I’d challenge any of them to cruise around a very choppy Solent at 35 knots like we did in the SEAir, transiting large ferry wakes at all angles, resolutely remaining on foil at a consistent ride height and handling in a way that did not unsettle passengers more used to conventional powerboats. SEAir has delivered a significant achievement.
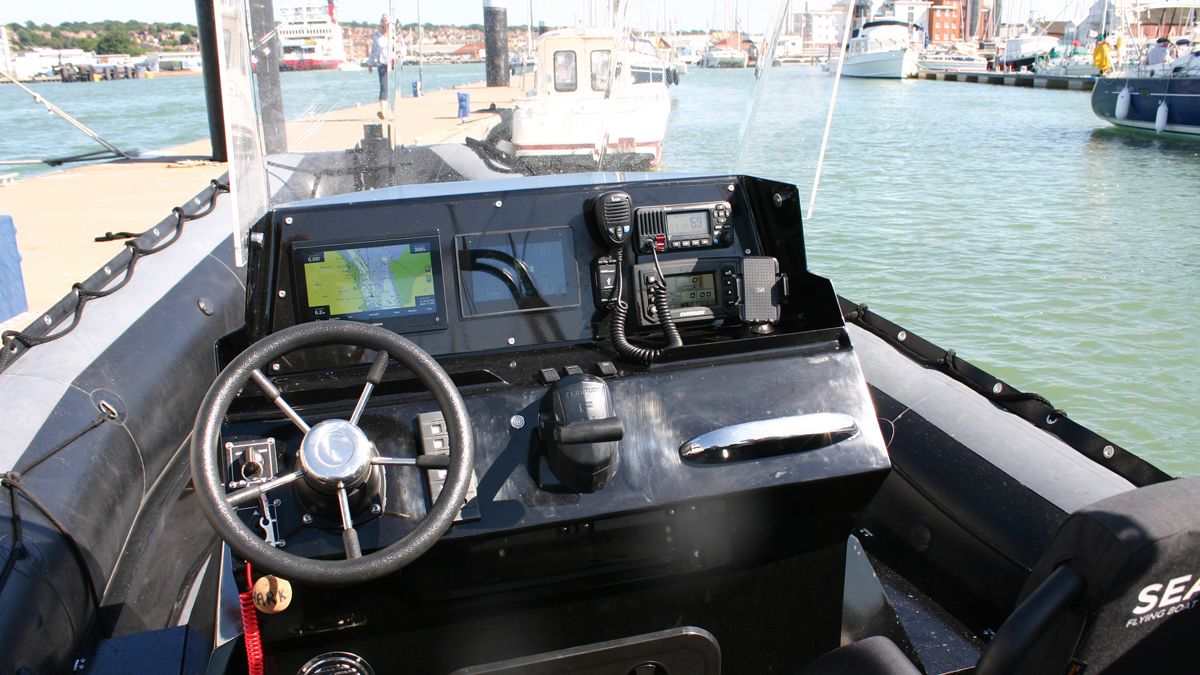
A pretty standard looking RIB console, but the tiny button to port of the throttle sets the foils to work
There are of course prices to pay for all this technology and not just in Euros. The boxes containing the foils and control actuators that make it all work cut across from the console to the tubes on both sides, affecting the boat’s interior usability.
The carbon fibre foils do not retract entirely flush with the hull, so berthing requires considerable care. A custom designed trailer allows the boat to be trailerable, but I would imagine it would also require more care.
At sub foiling speeds, the foils, even retracted as far as they will go, are just extra drag, so if you spend a day at 5 knots on the river in your SEAir you’ll burn more fuel than you would in a conventional RIB.
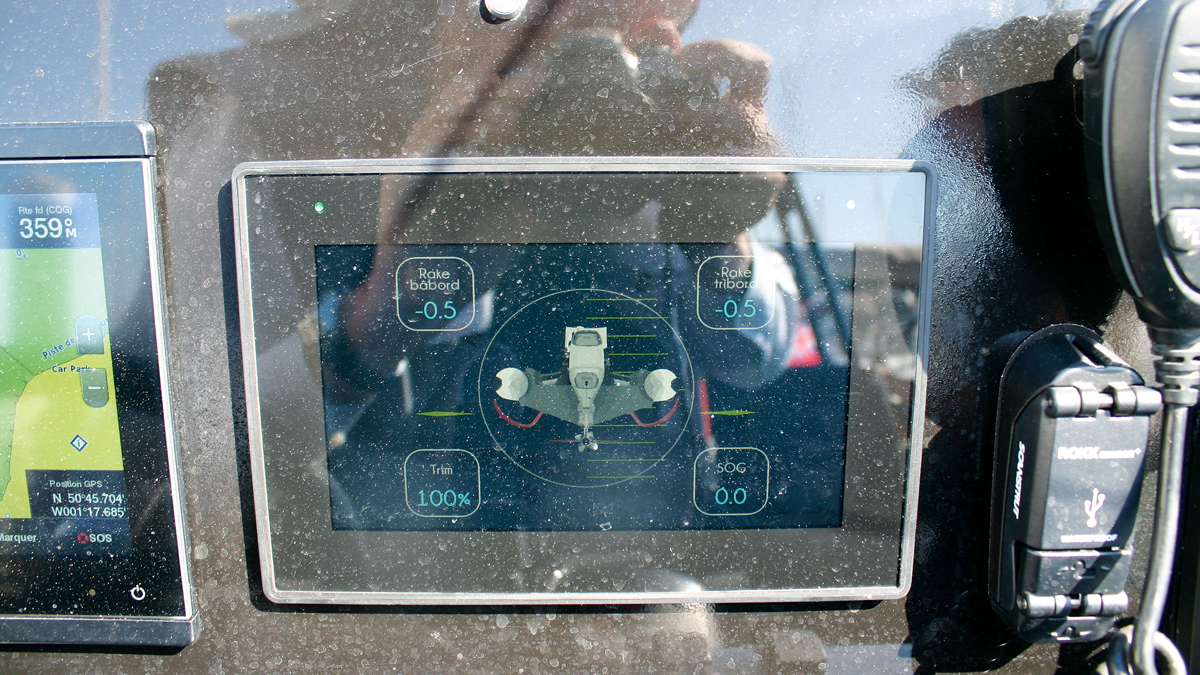
A foil status indicator screen sits centre stage on the dash
The big one for me though is foiling boats, because of where their centre of gravity is, naturally want to lean the ‘wrong way’ when cornering.
SEAir are working on this, as it’s not beyond their abilities to adjust the foils when turning so the boat leans into corners, and when they achieve this it should be incredibly manoeuvrable. At the moment, it is not.
Crystal ball
While it’s always a privilege to glimpse the future, I do wonder if the benefits of small hydrofoil boats will ever eclipse the downsides for most boat users.
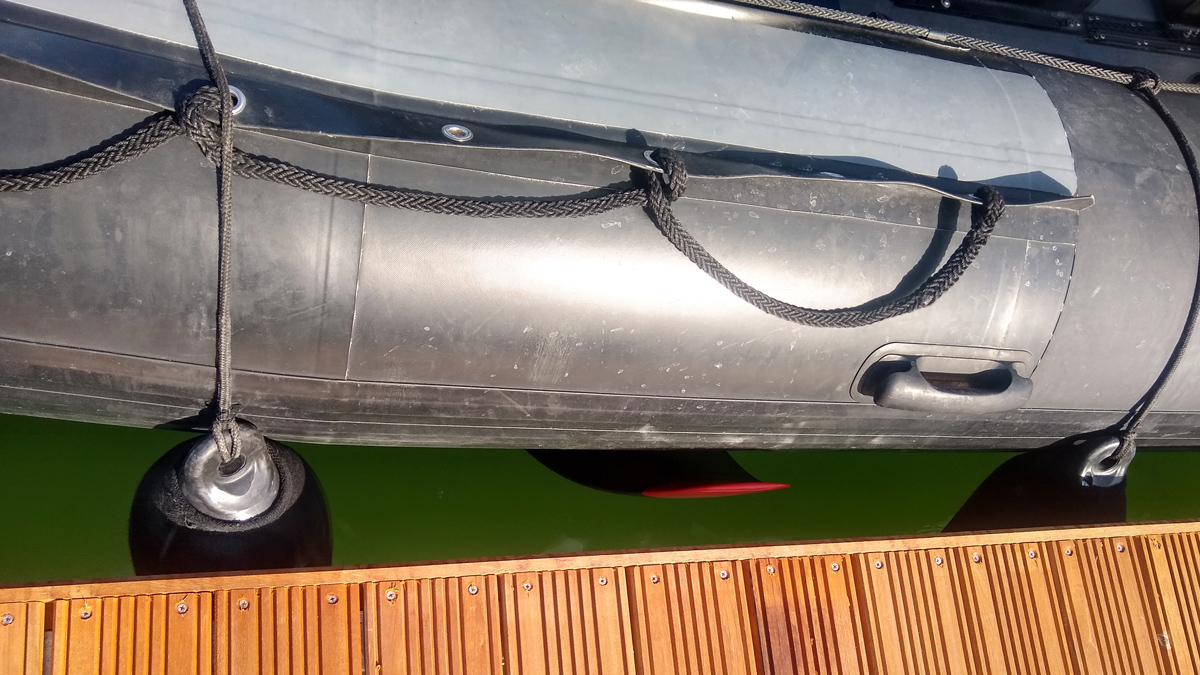
The carbon main foils in their fully ‘retracted’ position look somewhat vulnerable for berthing
I hope SEAir do well as they’re real enthusiasts with an ambitious and exciting project but my broader view is hydrofoiling RIBs are unlikely to ever be a big thing, simply because of the level of competence required to build them.
While the average boatbuilder in Canvey Island, Catalina, Concarneau or Calcutta can build a half decent planing vee hull, the calculations, composites, marine engineering and digital skills required to get a boat reliably foiling represent a real barrier.
Thanks to Speed@Seawork, a commercial and military fast craft sea trials day held at Cowes each year, for enabling this experience.
Why not subscribe today?
This feature appeared in the October 2022 edition of Practical Boat Owner. For more articles like this, including DIY, money-saving advice, great boat projects, expert tips and ways to improve your boat’s performance, take out a magazine subscription to Britain’s best-selling boating magazine.
Subscribe, or make a gift for someone else, and you’ll always save at least 30% compared to newsstand prices.
See the latest PBO subscription deals on magazinesdirect.com